Among newbies and seasoned welders, spatter is considered a serious nightmare. So learning how to reduce spatter when flux core welding is crucial for everyone.
Today, I’ll walk you through the actual causes of spatter, including the way of reduction and prevention. This might be your lucky day.
What is Spatter
During a weld, you may notice some small metal balls that are melting over the material you’re welding. Yes, that’s called “spatter.” It generally occurs while molten metal starts spatting all around; the name speaks for itself.
And the worst part is that the spatter usually gets stuck quite firmly to wherever it contacts. Thus, it dramatically turns your workpiece into a place of junk or mess.
What Causes Spatter
There are a lot of different causes of spatter. Some of them are as follows:
- Inappropriate Settings
One of the main reasons why you end up with a spatter is incorrect settings. Everything must be set to the correct rate from voltage to amperage to complete the welding application without any spatter.
Keep in mind that the level of the spatter may turn higher in case the voltage is too low. Besides that, if you set the amperage too high, you’ll have to deal with excess spatter.
- Surface/Workpiece Contamination
Oil, paint, stubborn dirt, and rust – are considered one of the main culprits behind the causes of spatter. Many of us deal with such an issue by not being careful about cleaning up the surface.
Yes, you must use any wire brush or a piece of rag to clean the workpiece before you start welding a piece of metal.
- Poor Quality Filler
Unsurprisingly, the cheaply-made filler material can make your welding project a nightmare. Even I have seen so many welders who had to close the welding project in the middle just because of excessive spatter, which causes due to the usage of poor filler material.
So try to spend a bit more extra bucks on the top-quality filler to get rid of that issue.
- Incorrect Shielding Gas
Although it’s not that common among welders, you still may end up with excessive amounts of spatter by choosing the poor shielding gas. Never use 100% CO2 if you want to weld through flux-cored shielding wire, as it will create lots of spatter.
Instead, use 75% argon and 25% Co2.
Do Flux Core Welding Generates Spatter
To be honest, yes. Flux core tends to produce lots of spatter while welding any metal. But that won’t happen at all if you utilize everything properly.
For instance, you should avoid high amp, low voltage, poor shielding gas, and cheap consumables to eliminate excess spatter production; there is no rocket science.
How to Reduce Spatter while Flux Core Welding
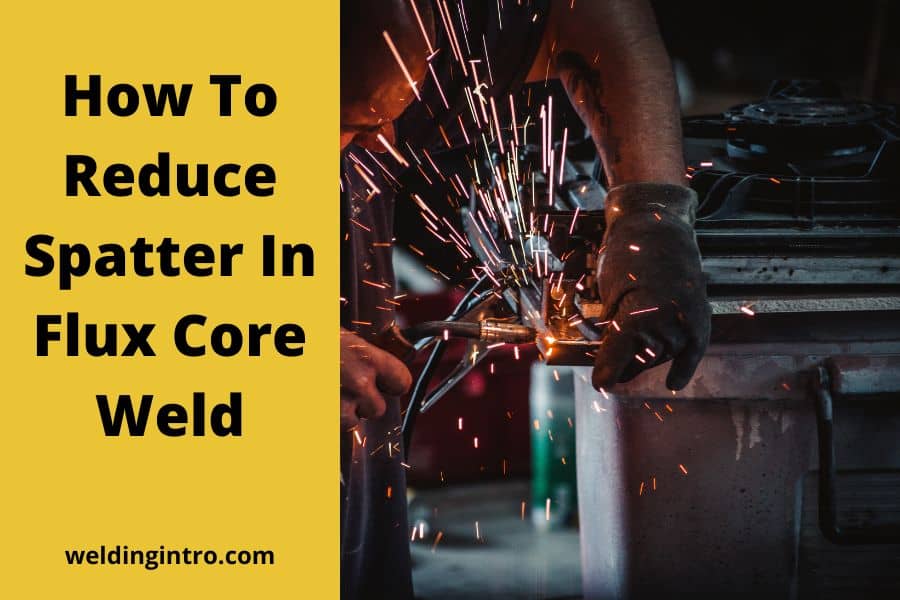
Here, I’m going to give you 5 suggestions to reduce spatter as much as possible during flux core welding –
- Be Careful About the Parameter
Yes, you can’t overlook the correct voltage and amp range during flux core welding, no matter what.
As I’ve said earlier, the rate of voltage shouldn’t be too low, and similarly, the amp rate shouldn’t be so much higher. Ensure to make their right uses by taking experts’ advice.
- Avoid Poor Filler and Consumables
There is no chance that you can accomplish any flux-core shielding wire applications using cheap consumables or fillers.
As flux-core itself is pretty much affordable, don’t think twice about spending a bit more dollars on high-quality filler materials and consumables for the best outcome.
- Clean Up the Surface before You Weld
Even if you use quality consumables, gas, or the correct amp, still spatter-issues may occur in case you don’t clean the surface before welding.
So you must eliminate the debris, oil, rust, or such things using a cleanser or a piece of rag.
How to Prevent Spatter
Preventing the spatter isn’t easy as ABC. However, following the correct guideline allows you to do this. So check it out –
- On every side of your weld, you must take off oil, rust, or such things. Sometimes, a typical rag may not work. In such a case, using a flap wheel, wire brush, and grind might be a good decision.
- Don’t be a fool by jumping into the welding process straight away. Always check the users’ guide before you weld the material to avoid every kind of risk, especially spatter.
- Don’t RUSH during flux-core welding, even if it becomes lengthy.
- Make the right use of every single piece of equipment. Avoiding improper shielding gas, cheap consumables, and inconsistent current can help you prevent the problem.
- In order to keep the spatter from sticking to the surface, feel free to use an anti-spatter gel or spray before starting welding. Trust me; getting rid of those pesky blobs really comes in handy.
Last Words
So that was everything on how to reduce spatter when flux core welding. By following this guide, you can eliminate the particular issue once and for all.
Nonetheless, always pay focus first on preventing the spatter issue. After all, prevention is better than cure; what do you think, eh?
Related Article