Within the realm of welding, the linchpin of any manufacturing process is Quality Control (QC), playing a central role in achieving sound and reliable welds. The collaboration between Quality Assurance (QA) and QC is essential, not only for meeting specifications but also for minimizing rework and ensuring the longevity of the final product
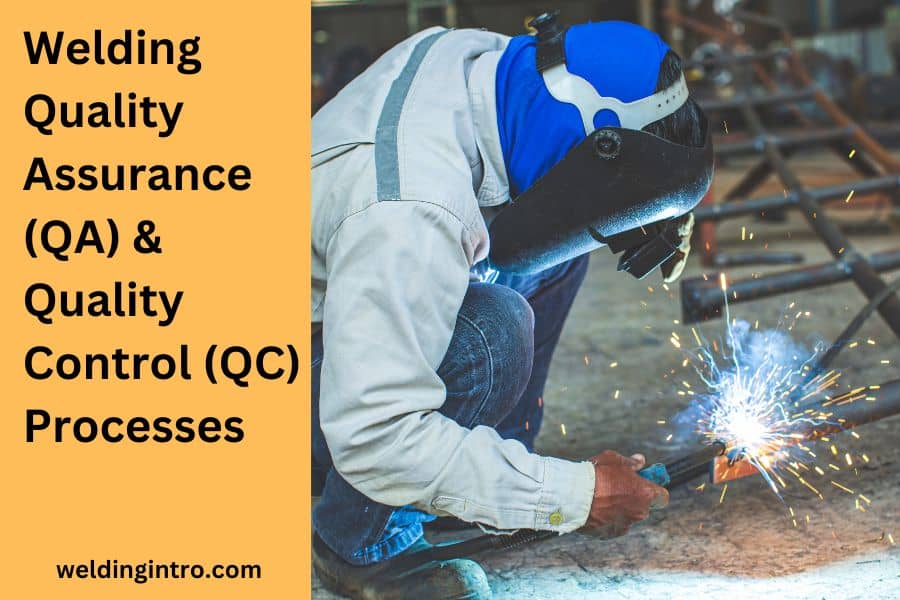
Quality Assurance: A Systematic Approach
Quality Assurance (QA) constitutes a systematic series of processes crafted for continuous monitoring and evaluation, ensuring the product’s quality. It serves as the foundation supporting a robust welding process, offering a framework for defined processes that establish systematic checks and balances, guarding against deviations from the desired quality standards.”
Quality Control: Confirming Compliance
Contrastingly, QC serves as the pulsating core of the production line, verifying the product’s alignment with specified standards. It encompasses thorough examinations and testing not only of the final products but also of the manufacturing procedures.
The results of these tests undergo scrutiny against predefined acceptance criteria. When implemented during manufacturing, this approach promptly exposes defects, enabling quick rectification and adjustments to prevent further faulty output.
In welding, the interdependence of QA and QC takes center stage in ensuring the creation of sound and reliable welds. Deviations from these procedures can lead to cascading consequences
Why QA/QC is necessary
In fabrication, a customer may specify the compliance to certain standards and specifications which the fabricator must follow. In some case it is so mandatory that, the welder must comply with the standards and follow the code. Negligence of such compliances may void the contract and even legal lawsuit may be imposed on fabricator as a penalty.
So ensuring QA/QC is very important for fabricators to create quality and non-defective welding. And all the fabricator must understand the standards to professionally carry out a welding project.
Consequences of Neglecting QA & QC Procedures
The consequences of overlooking sufficient QA/QC measures during fabrication can be significant. It may result in the production of welds with varying levels of quality, requiring correction and consequently delaying the delivery of the final product to the customer.
Beyond the immediate impact on timelines, there is the potential for damaging the reputation of the fabricator. Non-compliance with standards outlined in contractual agreements regarding QA/QC requirements can lead to contractual disputes and legal penalties.
These repercussions are more probable if quality issues arise after fabrication, causing delays or, in more severe cases, product failure during use.
QA/QC Documentation
A Quality Assurance Plan (QAP) must be developed for testing and checking QA/QC during the fabrication process. In this plan, key roles are defined and assigned to responsible personnel, with the designing engineer playing a crucial role.
The engineer establishes the quality assurance and quality control parameters of the project based on standards and codes, creating a comprehensive document known as the Welding Procedure Specification (WPS).
This document encompasses all requirements, such as welding procedures, gas details, voltage and amperage range, electrode specifications, gas selection process, welding position, pre and post-heating requirements, polarity, current type, and more.
Qualification of WPS and Welders: A Prerequisite for Excellence
The qualification of Welding Procedure Specifications (WPS) and welders is a pivotal step in ensuring the capability to produce reliable welds.
Welder Qualification
Welder qualification is a crucial process that ensures welders possess the necessary skills and expertise to produce high-quality welds in accordance with industry standards. The welder qualification process involves testing and assessing a welder’s ability to perform specific welding procedures, often in various positions and with different materials.
Successful welder qualification is often a prerequisite for obtaining certification, demonstrating a welder’s competency and capability to meet the demands of specific welding projects.
WPS Qualification
WPS (Welding Procedure Specification) qualification is a systematic process essential for ensuring the reliability and consistency of welding procedures. It involves a comprehensive examination and documentation of welding parameters, materials, and techniques to establish a standardized procedure for producing quality welds.
Qualifying a WPS typically requires thorough testing and evaluation, including visual inspections (non-destructive) and, in some cases, destructive testing. The goal is to validate that the welding procedure meets industry standards and specifications.
After DT (Destructive Testing) or NDT (Non-destructive Testing), result is qualified either as passed or failed. If passed, the quality of the weld is ensured and if failed, the fabricator must rework on the project to comply with the compliance. The results are documented in a Procedure Qualification Record (PQR) or Welding Procedure Qualification Record (WPQR).
On the other hand, if the project has pre-qualified welding procedure specification (PWPS), then further testing is not required.
Inspection and Test Procedures: Blueprint for Quality
To translate the WPS into action, Inspection and Test Procedures (ITP), check sheets, and test sheets are created based on design documentation. These documents serve as the guiding light during QC checks and tests, providing a comprehensive record of the entire process.
1. QC at Different Stages: A Comprehensive Approach
QC is not a one-time event; it is a comprehensive process that spans the pre-welding, during welding, and post-welding phases.
- Quality Control (QC) Before Welding:
- Material Confirmation: Prior to QC, it is essential to verify that the mechanical properties of the material comply with design specifications.
- Joint Preparation: Before QC, conduct dimensional and cleanliness checks to ensure the joint aligns with design specifications and welding standards.
- Welder Qualification: Confirm that the welder is qualified to perform the weld.
- QC During Welding:
- Temperature Checks: Verify that preheat and interpass temperatures adhere to the limits specified in the Welding Procedure Specification (WPS).
- Filler Material: Ensure that the filler material meets the requirements outlined in the WPS.
- Other Checks: Include cleaning between passes, assessing weld run appearance, and back gouging where specified.
- Confirmation of WPS Adherence: Ensure faithful adherence to the WPS during the welding process.
- Non-Destructive Testing: Perform tests as specified in industry standards.
- QC After Welding:
The extent of QC at this stage depends on the welding compliance standard, weld class, and customer agreement. Testing may involve Destructive Testing (DT) or Non-Destructive Testing (NDT)
Conclusion
In the intricate world of welding, where precision and reliability are non-negotiable, the importance of Quality Assurance and Quality Control is imperative. The consequences of overlooking these processes can reverberate far beyond the workshop, affecting timelines, reputation, and even legal standing.
By meticulously adhering to QA/QC procedures at every stage, welders and fabricators pave the way for not just meeting specifications but for crafting a legacy of excellence in welding.
Sources:
- https://blog.red-d-arc.com/welding/welding-quality-assurance-control
- twitraining.com/home/programmes-and-courses/welding-inspection/welding-quality-control-coordinator
- researchgate.net/publication/318110082_Quality_control_and_assurance_in_fabrication_of_welded_structures_subjected_to_fatigue_loading