There are several types of welding joints, each designed to meet specific requirements and suit different applications in various industries. Many people mistake weld types as weld joints but both are different. There are a number of differences between weld type and weld joints.
So, it is important to distinguish between weld types and weld joints. There are many weld types like filet weld, groove weld, plug weld, surfacing weld, slot weld, flash weld, seam weld and so on. We have discussed weld types in separate articles in detail.
On the other hand, there are 5 types of weld joints according to AWS (American Welding Society).
They are
- Butt joint
- Corner joint
- Edge joint
- Lap joint &
- Tee joint
Let’s describe them in details

What is Weld Joint
A weld joint refers to the specific area or configuration where two or more pieces of metal are welded together. The metals can be similar or dissimilar. If the weld joints are strong then the weld is considered as strong. Several factors contribute to the weld to be a good weld. Weld joint design is one of them.
To meet the quality standard, weld type must comply with the weld joint design. For examples-
- In groove weld type, butt joint is suited
- For filet weld, tee joint is best
- For both filet and groove, corner joint can be used
Butt Joint
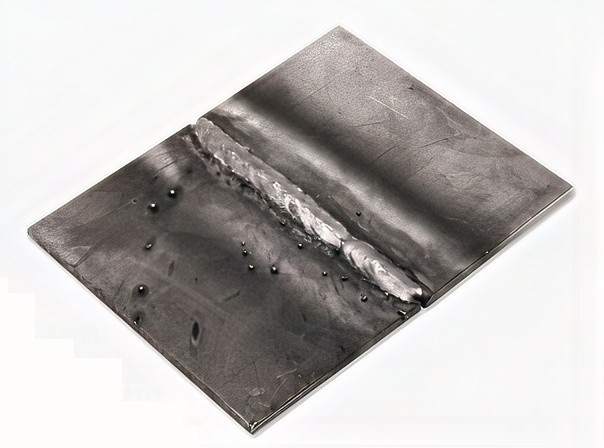
In a butt joint, the two pieces of metal to be joined are aligned in the same plane, and welding is done along the edges. This joint is commonly used for joining flat pieces, providing a strong and clean connection.
Butt joints are widely used in various welding processes, including arc welding, MIG (Metal Inert Gas) welding, TIG (Tungsten Inert Gas) welding, and others. There are few ways you can design butt joints. They are-
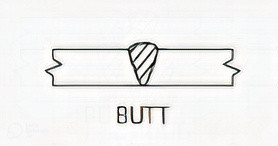
- You can butt joint either with backing or without backing or open root. Here a backing is a material or device used to support the molten weld metal and prevent it from flowing through the joint or creating a hole on the opposite side.
- The edges of materials used in butt joints can be beveled or square grooved. Beveled joints are stronger than square grooved joints but very time consuming than beveled joints. Materials can be partially or fully beveled and you may need to prepare both workpieces for beveled angles. For example v-groove edges.
Pro Tips
Determine whether the materials require preparation for deciding whether to use bevel or square groove. Also you should determine whether to use root opening or fit up process for better weld.
Examples Of Butt Joint
- Single U-groove
- Double U-groove
- V-grooved weld
- Beveled (full or partial)
- Square groove
Lap Joint
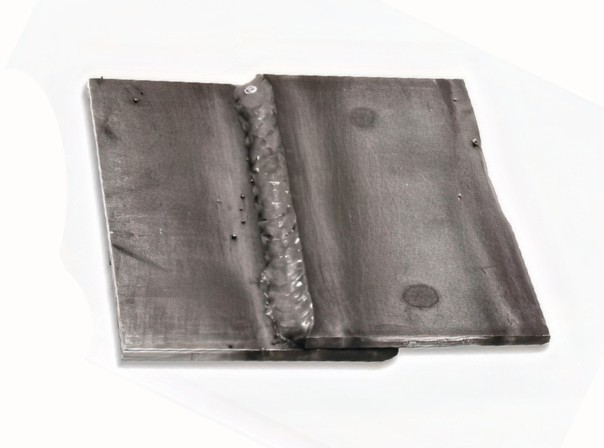
For lap joints you need to put metal pieces upon one another in an overlapping pattern. This type of joint is used rarely. It is mostly used in welding metals of different thickness together. This type is not suitable for welding thicker metal while perfect for thin or sheet metal.
It can create a 0-5° angle when put on one another. You may weld on both sides or one side. This type of joint may produce corrosion owing to its overlapping position however you can reduce that by applying correct welding technique.
For the best flush contour you should go for butt joint. Lap can provide stronger joints in high stress work but can’t provide that level of contour.
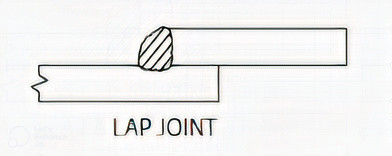
Tips
- Make sure there is no gap between the sheet metal pieces while welding
- Reduce the amperage of welder and use faster travel speed while welding thinner metal
- Weld both sides for rigidity
Style Of Weld
- Plug weld
- Bevel groove
- Flare bevel groove
- J-groove weld
- Slot weld
Corner Joint
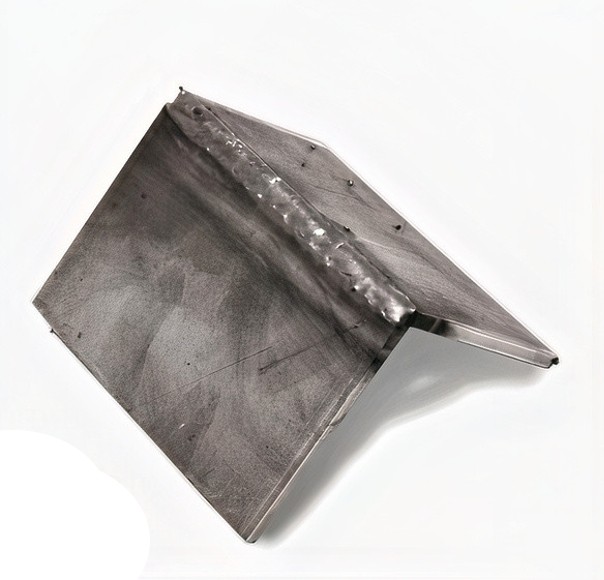
A corner joint is a type of joint used in welding where two workpieces meet at right angles, forming an “L” shape. This joint is commonly found in various welding applications and is used to create structures with perpendicular members. In a corner joint, the weld is typically applied along the outer edge of the joint, joining the two pieces at the corner. You may use the joint to make a table or any other square frame.
Though this joint requires little metal preparation, proper preparation can make a strong weld. This may involve cleaning the surfaces, beveling the edges, and ensuring proper fit-up of the workpieces.
There are two types of corner joints. Open corner and closed corner. When one edge is closest to another corner it is a closed corner joint. And when there are openings between the joints, it is an open corner joint.
You must take the thickness of metal into consideration while choosing between open or closed joints. If the metal is thinner, you may need to increase the travel speed to avoid burn through problems. And in case of thick metal you need to increase the deposit rate to penetrate the metal. Also keep in mind that,

You need to prepare the workpieces in joining the metals into 90 degree angles. In this case make sure the edges of the workpieces are cut in square to avoid distortion.
Pro Tips
- Increase travel speed while welding thinner metal.
- Ensure the workpieces fit each other while making v-groove joints.
Edge Joint
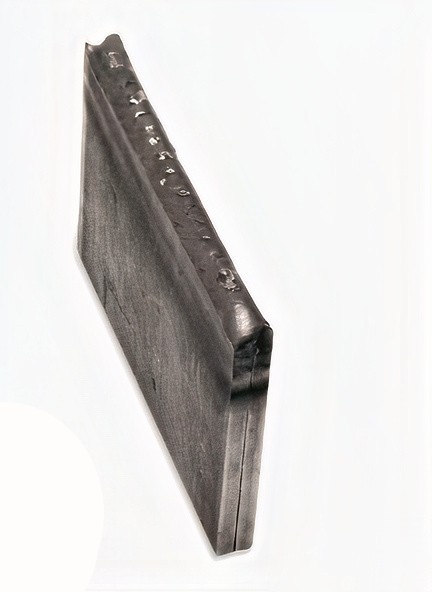
Edge joint is a type of joint where two pieces of metal are placed together matching the edges. And then welding is applied to join the pieces together. You may put the pieces flat to each other or may bend them a little bit making an angular joint.
In this joint, surface stresses are distributed over the entire metal pieces thus enabling it to withstand the force and retain integrity in finished weld.
You need to prepare the surface before welding in case of edge joints. You can make the edges like V grooved, U-grooved, Square groove or J-grooved depending on the material type and its thickness. Doing so basically ensures the deep penetration consequently making a better weld joint.
Now you may mistake considering edge and corner joints as similar. Yes, both are similar to some extent. Edge joint focuses to weld inside of the material while corner joint does weld outside of the workpiece. Which one to use depends on the material thickness and application.
You may easily grind the outside of the edge joint to make it smooth and fine after welding.
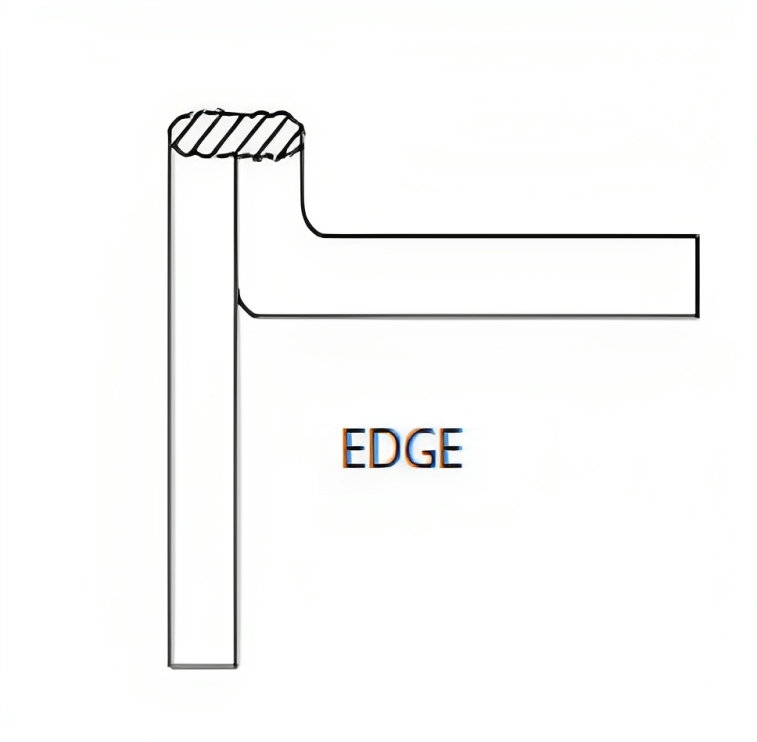
Welding Style
- U-groove
- V-groove
- J-groove
- Square groove
- Bevel groove
- Edge flange
T-Joint
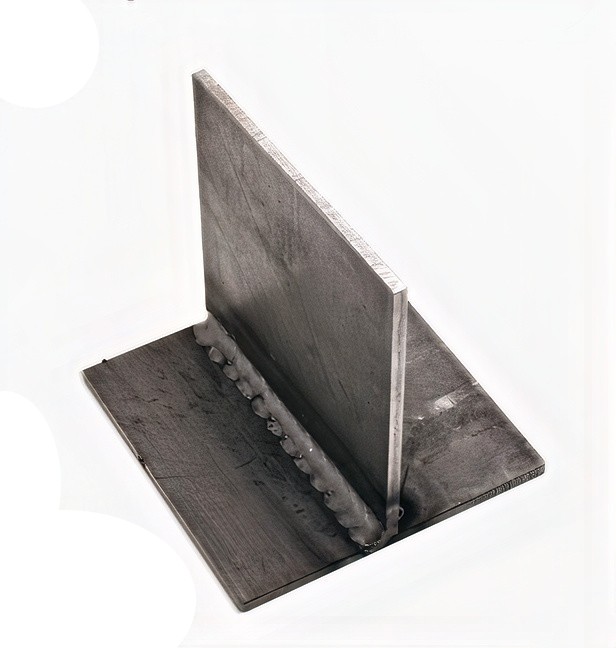
From the name we can imagine the type of weld joint. T- joint is joining one piece of metal in a perpendicular position over another flat metal piece. This type of joint creates a 90° angle over one another.
In other words we can say T-joint is placing one edge of a metal over another metal plate. To perfectly make the joint you must smoothen the edges of the metal so that there is no gap between the metals.
It is a widely used joint in fabrication and also holds stronger joints. Welding both sides will provide extra strength to the joint avoiding the stress. If you are joining a thicker and a thinner metal using the joint type, you must focus more weld on the thicker side for better penetration and better joints.
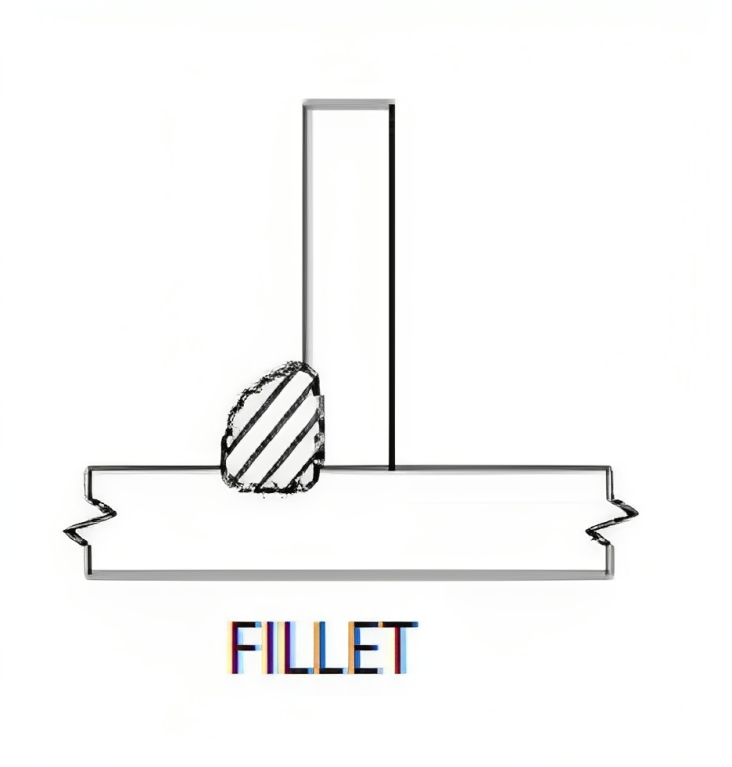
Tips
- Split the 90 degree into 45 for ensuring best penetration
- Weld from both sides to make the joint stronger
Welding Style
- Fillet weld
- Bevel groove weld
- Flare bevel groove
- J-groove
- Plug and slot weld
Lastly
Above are the different welding joints that welding students or any diyer’s must know. If joints are unknown to anyone, better weld penetration moreover aesthetic weld would be difficult to get.
Check out posts on