Can you do MIG weld thin wall tubing? Following MIG welding for thin wall tubing is fine if you use small-diameter wire. Minimal heat is needed to melt the wire.
But why should you not use thicker materials? The excessive heat will cause a distortion in shape thus spoiling the welding. Need to learn in details-
Then let’s learn how to MIG weld a thin wall tubing in detail-
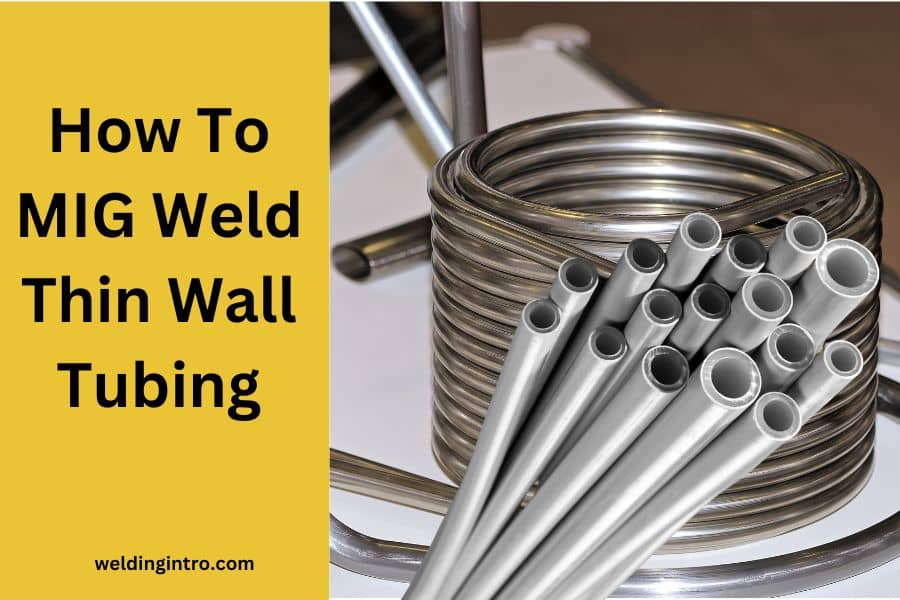
What Is Thin Wall Tubing?
Thin wall tubing is a precision tubing that has several functional properties. Its dimension is smaller than other tubing’s, ranging from 0.001-inch to 0.065-inch.
Manufacturers either use plastics or metal to fabricate thin wall tubing. Usually, they use Teflon, PET, PVC, or Nylon plastics.
Alternatively, different types of metals can be used for this tubing. For example stainless steel tubing. These type of metal tubing are used in low pressure applications where you need low temperature and heat to mig weld stainless steel tubing.
What Type Of Metal Is Used In Thin Tubing?
Copper, stainless steel, brass, steel, and aluminum are the top material used for thin wall tubing. However, stainless steel and aluminum alloys are the most widely used. But many metals come in several grades
The inner diameter thickness of the wall has an impact on the thin tubing. But it doesn’t affect the external diameter.
What Type of MIG wire to Use for Welding Thin Wall Tubing?
Bare wire is the best choice to use for welding thin wall tubing. After all, it does not have excessive special additives. This reduces the likeliness of getting combat rust or dirt.
Additionally, a bare wire has an excellent ability to weld at low currents. The filler wire will be only added it is necessary.
And if you ask what mig weld machine to use, then the answer is any highly efficient mig welder that can weld with thin mig wire and where feed speed of motor can be lowered at a specific volume.
How To Mig Weld Thin Tubing (Step by Step)
Ever wondered how to get a good result when doing MIG welding on thin wall tubing? We have broken the steps into 5 sections. Follow these steps to successfully MIG weld square thin tubing.
- Step: 1—Fit-up
First, gather the metal pieces and lay them out on a bench, depending on how you want to join them together. The mitered, corned and straight pieces should fit appropriately.
Measuring the metal pieces more closely is worth taking a little more time. It will pay you back when you are less likely to blow holes through your project. It will distort less overall.
- Step: 2—Test Settings
The next thing is testing out your settings. Following the chart or built-in settings in the machine seems more appropriate to get a baseline.
However, it is a solid rule of thumb to run a practice weld first. After all, no pro athletes brag about playing the game. They practice heavily.
You should also approach your welding and do a little practice on some scrap material that has a similar thickness. It will make sure everything is going okay during the welding.
- Step: 3—Know Your Joints
Understanding what type of joint you will weld is crucial because different metal has different physical properties. Usually, four types of joints are available for square thin wall tubing: the Mitered corner and three types of joints on the side.
Butt joints are located where the material is butted against one another. It is best just to drag the welder along and follow the seam moving at a relatively steady pace.
But when it comes to welding the outside corner joint, it has a chance to melt through on you due to its thin material. The best approach is using the weld vertically down. It will help you to move more quickly. You will not build up too much material. You will penetrate in just fine.
Finally, you need to point the weld at 45 degrees for the inside corner joint and move along with the weld puddle all the way through. But remember, the corner of the piece will absorb more heat than the edge. Focus more on your welding position and let it bridge over.
- Step: 4—Use a Good Welding Technique
Stick out how your contact tip is away from your work. Keeping the distance short is crucial. Also, pay attention to your work angles relative to the two pieces you are welding together.
Also, you can’t ignore the travel angle of the weld. Either push or drag, but don’t get carried away. Usually, 10 or 15 degrees appear enough.
Also, your travel speed should be tied into both plates without sagging or burning through. Keep moving your weld but don’t overdo it. Watch out for the weld puddle, and let that guide how fast you are moving through.
- Step: 5—Weld Sequence
The last task is sequencing your welds to reduce the amount of distortion. Fillet welds will pull more than groove welds.
When you go to weld for these joints, make sure to weld the ones that will distort the least. It is a good idea to weld from the inside to the outside. This will help keep your parts from warping and distorting all out of shape.
What To Consider For MIG Welding Thin Wall Tubing?
When it comes to MIG Welding on thin wall tubing, you can’t overlook some crucial aspects.
1. Filler Metal Selection-MIG Wire
Choosing a low-temperature filler metal is best for welding thin wall tubing. Also, ensure it is compatible with design requirements, regulatory specifications, and codes.
2. Heat Control
When welding thin wall tubing, imbalanced heat can affect the welding results. Keep the amperage and voltage settings lower and increase them gradually if needed.
3. Consistency
You can’t achieve nice and smooth welding until you maintain consistency. Your welding position, movement, pressure, gliding, and motion —everything plays a key role.
4. Perfect Fit
Before welding the workpieces, ensure they fit perfectly on the corners or sides where you want to join them. Otherwise, the welding result will be unstable.
Conclusion
When it comes to MIG welding thin wall tubing, you need to practice appropriately before finally welding the workpieces.
Ensure you have all the Welding equipment, compatible shielding gas, and filler metal. Plus, the mechanical properties of both items you want to join should be matched.
Also check