Almost every seasoned and hobbyist welder is familiar with MiG welding. It’s ideal for numerous projects, especially for joining different materials with a mig welder machine within a snap.
But can you MiG weld railroad tracks?
Well, starting from excellent welding speeds to maximum precision, you can get so many benefits by applying MiG welding. But unfortunately, the thickness of railway track metals is different, and chances are it won’t make a perfect match with MiG welding.
So if you think Mig welding isn’t your cup of tea in terms of welding railroad tracks, then don’t worry since there are some effective methods available for you.
Can You Mig Weld Railroad Track
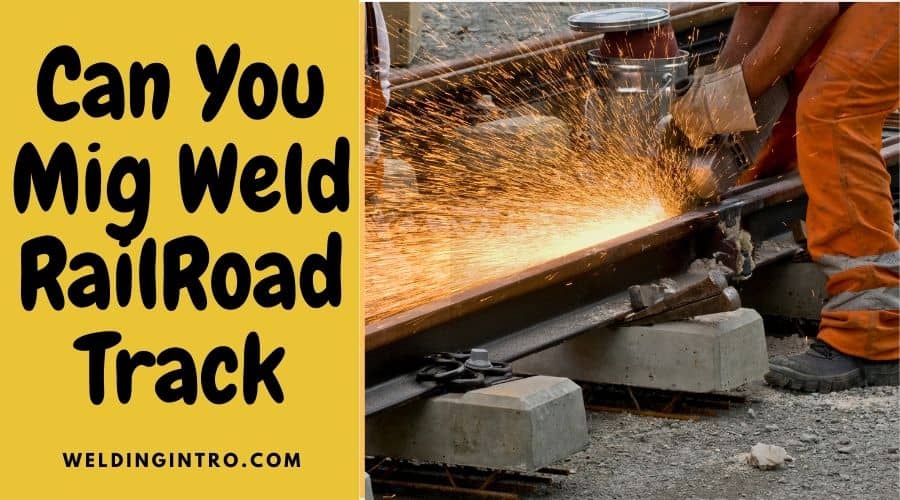
You might be the biggest fan of Mig welding, but that doesn’t mean it has to be ideal for welding railroad tracks, right?
As you know, Mig welding is only compatible with the thickness of 24 gauge. But railroads are manufactured with extremely stronger and thicker metals.
So, you won’t be able to join two rail connectors or the 2 thick metal pieces as firmly as required. If do so, the result can be negative.
What are the Requirements to Mig Weld Railroad Track?
To be frank, Mig welding can’t be your go-to process while you’re preparing to work on rail roads because of the thickness of the metals & the existing gas involved. You will need numerous gas or spool wires to work with various kinds of metals.
However, if you are determined to use mig welding technique for railroad metals joining, then you should follow a few requirements. These won’t help to fuse the railroads efficiently but will give some push in the work.
Take a look at some of the requirements to Mig weld railroad track:
- Closely look at the type of materials. Mig welding suits mild steel, magnesium, and aluminum more often. Rail tracks are mostly carbon steel and mig is compatible with the metal.
- As I’ve said before, Mig welding is able to weld a material that’s 24 gauge thick. So if you’re going to work with thicker metals, you should increase the heat input of the machine to make the metal penetrate as deeply as possible. And preheat the metal before starting to weld.
- According to the experts’ opinion, Mig welding should be done only indoors as wind may interfere with the gas, which causes negative results. If you are determined to use mig outdoors in railroad tracks, make sure you have arranged sufficient gas and proper ventilation.
Different Welding Types for Railroad Track
I have already been told that mig welding is not suitable for railroads. There are few welding types suitable for joining railroad tracks.
They are-
Flash Butt
This is a pretty common name among welders, especially to those who don’t want to weld railroad tracks by applying any fancy techniques. While utilizing it, all you need to do is set up the two metal pieces carefully end-to-end and start welding following the connection.
It is suitable to weld any workpieces that are thicker like rails, anchor chains, and pipes.

Advantages
- It ensures excellent welding quality
- The toughness of each weld joint will appear to be good enough
- One of the most versatile and simplest types of welding
- Much better for either base rail or factory rail welding
Disadvantages
- Flash butt requires heavy-duty power supply and generator to run
- While welding, rails may burn extensively at times
- It is slightly expensive
Gas Pressure Welding
As the name suggests, this welding process uses the actual power of heat that’s produced by any gaseous fuel. It usually consists of acetylene cylinders, oxygen, piping & pressure regulators
Speaking of the range of temperature, gas pressure welding generates nearly 3600°C in order to melt metals quicker yet maintaining a firm bond.

Advantages
- It only requires a single investment to get the job done
- Unlike the typical welding processes, it takes less time
- The burnout of steel rail will be minimal
- One of the perfect choices for the welding that involves “on-site joint”
Disadvantages
- Joint sections of each track will seem to be quite strict while welding
- Not that easy to control, especially for those who are new in gas welding
Thermite Rail Welding
According to my experience and personal opinion, thermite rail welding (TW) is the most effective method for the tracks of railroad. Also familiar as exothermic welding, it plays a significant role in melting metal in order to join every conductor permanently.
Compared to other choices, it ensures optimal resistance against corrosion.

Advantages
- Allows you to make a firm joint at a minimal production cost
- Ensures optimal mechanical strength and resistance against corrosion
- Pretty easy and straightforward to operate
- Ideal for repairing on-site joint, broken rail steel, and massive transportation tasks
Disadvantages
- Can be less economical when you go for welding light parts or cheap metals
Which Welding Type Is Best for Railroad Welding and Why?
So many welding types or techniques can be found when you look for railroad track welding. All of them have some pros as well as cons. So all of them can not be the best option to choose from.
After accomplishing brainstorming research, I can confidently say that thermite rail welding is a far better option to go for railroad welding.
It has something that makes it much better than the other. These are some of the reasons behind it:
- Easy-Peasy Application
Unlike the mainstream welding methods, thermite welding is easier and less challenging, especially to those who are new in the field of fabrication. Many people, especially newbies, prefer something that can be operated or utilized easily.
- Setup Cost is Low
If you can get a job done without spending extra bucks, then why to spend an additional pretty penny?
You might be a fan of flash butt due to their excellent welding quality. But it’s equally true that it’ll hurt your wallet.
In this case, you can finish the job within a low budget by applying thermite welding technique.
- Needs No Power Supply
You heard it right!
It can be annoying or tiring at times to arrange an extra power supply or generator for railroad welding. But guess what? Thermite doesn’t even require such things at all. You can do the job applying less amperage of power.
- Highly Corrosion-Resistant
The corrosion is a common problem unless you use thermite welding. With the help of excellent mechanical strength, it can give as much protection as possible against corrosion, allowing you to have a safe and effective rail section for a long period.
Frequently Asked Questions
1. Can railroad rails be welded?
Absolutely! Railroad tracks can be welded using specialized welding techniques. For example Thermit Welding Flash butt welding.
2. Can you weld railroad track to mild steel?
While it’s technically possible, it’s not a recommended practice. Railroad tracks are typically made of high-strength steel, and welding them to mild steel might lead to compatibility issues and compromise the structural integrity.
3. What is the temperature for welding of rail?
Welding rail tracks usually involves high temperatures. The specific temperature depends on the welding method used, but it typically ranges from 2,500 to 3,000 degrees Fahrenheit (about 1,370 to 1,650 degrees Celsius).
4. Which iron is used in railway track?
Railway tracks are primarily made of steel, not iron. The type of steel used is often high-carbon steel due to its strength and durability to withstand the heavy loads and constant stress from passing trains.
5. Why do railway tracks not rust?
Railway tracks are indeed susceptible to rust, but they’re often made of steel alloys that are more corrosion-resistant. Additionally, regular maintenance, such as applying anti-corrosive coatings, helps prevent rust and ensures the longevity of the tracks.
Wrapping Up
Now you’ve got the complete answer of “can you Mig weld railroad track” in detail. Keep in mind, railroad track welding isn’t child’s play. There can be so many difficult tasks involved, and more importantly, applying the proper welding technique is the key to getting the optimal result.
So, stay safe and happy welding.
Related Articles