Underwater Welding is one of the most high-demanding professions in the field of welding. Even though welding itself is a difficult process, this one entails further risks and challenges. Still, many people want to build their careers in welding field, especially those who love to accept challenges and risks. This article will focus on the basics of Underwater Welding, its benefits, types and associated risks.
Lets start with the basic.
Understanding Deep Underwater Welding
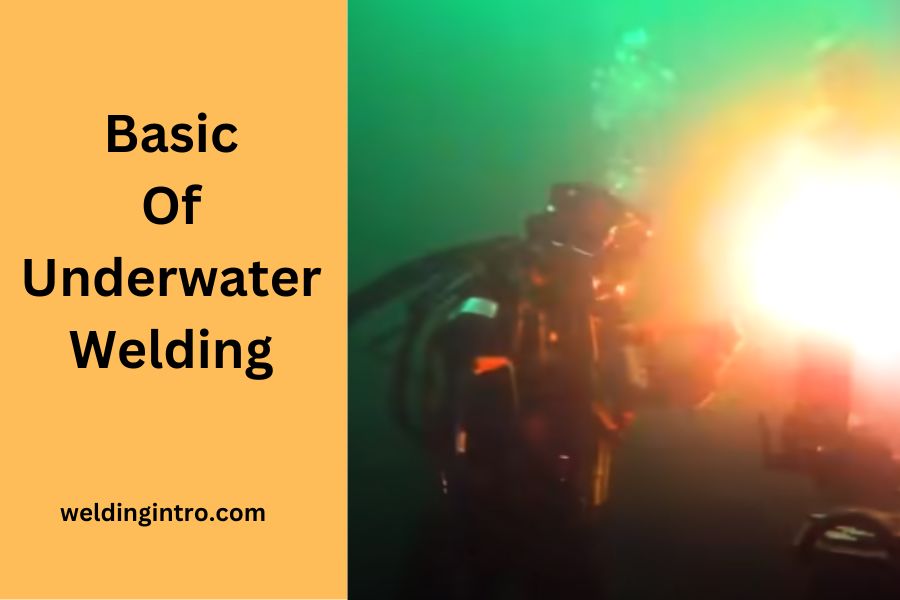
Like other welding methods, Underwater Welding also involves high-pressure welding mechanisms. But it differs from others in terms of ground. Underwater Welding requires skilled welders to dive into water to perform welding tasks.
The deep underwater welding process is familiar as deep underwater welding since welders conduct the whole process in between thirty to four hundred feet deep under salt water. It aims at maintaining and repairing marine structures.
However, Underwater Welding has two variations:
- Dry Underwater Welding
People perhaps mostly know this as Hyperbaric welding. A Russian metallurgist named Konstantin Krenov invented this technique in 1932. Since then, welders have been using this method for repairing pipelines, ships, offshore oil platforms, etc. This method is more prominent for welding steel materials.
Dry underwater welding is also conducted underwater but in a sealed chamber filled with shielding gas. Welders most often use Helium-oxygen-based gas mixtures inside the hyperbaric chamber. Since the welding structure remains isolated from the water environment, it is also familiar as “habitat welding.”
- Wet Underwater Welding
As the name implies, wet underwater welding requires the welders to conduct their tasks underwater. Therefore, welders remain exposed to a direct wet environment. Wet underwater welding is more risky and challenging than dry one. It becomes really difficult to retain the heat in the water, increasing the chances of defects such as cracking.
Besides, there are risks of getting electric shocks.
Dry Underwater Welding Process
Welders may use different processes for dry underwater welding depending on the hyperbaric chamber’s size. The leading methods are as follows:
Habitat Welding
Welders mainly implement habitat welding for hot tasks. The key characteristic of this method is that it does not require larger chambers. The inside pressure of the chamber is maintained a bit higher than the outside pressure for transporting toxic welding gases outside and preventing combustible hydrocarbons.
Dry Chamber Welding
It is almost akin to Habitat welding, requiring smaller chambers for maintaining a drier ground for welding in the world of water. However, the main difference is that the chambers of this welding only fit the welders’ upper body instead of the whole body.
Gas Tungsten Arc Welding
This method is more popular as Tungsten Inert Gas or TIG welding. It is one of the most used methods for dry underwater welding. In this process, welders use a melt-resistant tungsten electrode to generate the arc. Welders most often use Helium or argon gas as the shielding gas. TIG welding is famous for its high-quality and precise welding outcome.
Therefore, welders widely use this method for structural applications.
Gas Metal Arc Welding
Gas metal arc welding or GMAW has two variations: Metal Active Gas (MAG) welding and Metal Inert Gas (MIG) welding. Here welders use a consumable metal electrode to create the arc for welding. The method involves a welding gun that automatically feeds the filler wire and pumps a shielding gas to protect the weld area.
The type of shielding gas can vary depending on the MIG or MAG process implemented. In the case of the MIG process, helium or argon or their mixture gas act as inert gases.
In contrast, carbon dioxide, mixtures of argon, oxygen, and carbon dioxide can serve as shielding gas.
Pressure Welding
This is a solid-state welding that requires no external filler materials. The methods for pressure welding include resistance welding, explosion welding, gas welding, diffusion welding, ultrasonic welding, and friction welding, etc.
Advantages of Dry Underwater Welding
Some of the major Advantages of dry underwater welding are as follows:
- It is safer for the welders since the welding environment remains separated from the current of the water and marine animals.
- Dry underwater welding generates more premium quality welding outcomes due to lower levels of hydrogen and the absence of water in the welding environment.
- Dry environment facilitates Non-Destructive Testing
- Welders can easily monitor the pipe alignment, joint preparation, and other surface requirement.
Process of Wet Underwater Welding
In wet underwater welding, welders manually conduct the welding tasks as they do in the open-air field. This welding method requires a special electrode to complete the welding. The welder is connected to the surface-mounted power supply using cables and hoses.
However, this method depends on the existence of sufficient gaseous bubbles around the arc. The bubbles work as insulators to protect the weld area by preventing electrical conduction through the water. It may seem beneficial for the welders’ safety, but it creates additional hazards for the welders to complete the weld.
Shielded metal arc welding, Flux-cored arc welding; Friction welding are some of the most prominent processes for wet underwater welding.
Understanding Underwater Shielded Metal Arc Welding
Shielded metal arc welding (SMAW), also familiar as Manual metal arc welding, is one of the most used methods for wet underwater welding. It involves creating an arc between the workpiece and a shielded metal electrode. Welders can use one of the three types of electrodes: Cellulosic, Rutile and Basic.
In this process, the metal rod and workpiece melt-down to develop the weld. Their simultaneous melting develops gas and slag that will protect the weld pool from oxygen and nitrogen in the atmosphere.
Advantages of Wet Underwater Welding
Some of the leading advantages of wet underwater welding are as follows:
- Wet underwater welding is a versatile and cost-effective procedure.
- Wet underwater welding requires less time compared to dry one.
- Welders do not need to build any enclosure which makes the whole procedure faster.
- It is easy for the welder to move in the water.
Polarity and Settings of A Welder In Underwater Wet Welding
Since underwater wet welding is more prone to induce electric shocks, welders must focus on the polarity and proper settings to avoid such accidents. If you work as an underwater wet welder, never ever use Alternating Current (AC) for welding.
Otherwise, handling the situation can become too difficult in case of an alternating current shock. Direct current straight polarity will be more convenient for wet underwater welding. When the electrode is negative and the plates are positive, straight polarity takes place.
Here is the Commercial Electrode Chart (Waterproof):
Size | Commercially prepared waterproof electrodes | Specification |
1/8’’ Anderson easy weld #1 | Carbon Steel (E7014) | – |
1/8’’ BROCO Sof-Touch | Carbon Steel (E7014) | – |
1/8’’ BROCO SS | Stainless Steel (E3XX) | – |
Risks Associated With Deep Underwater Welding
Deep underwater welding involves numerous risks, including:
Electric Shock
Water is a good electrical conductor. Any defective equipment that is not sufficiently waterproof can make the welders more vulnerable to electric shock.
Explosions
The oxygen and hydrogen mixture develops numerous gas pockets which can lead to explosions if ignited.
Drowning
A faulty oxygen tank, mask, or other equipment can result in drowning. Besides, underwater obstacles, less visibility can make bigger trouble for the welder in the deep water.
Hearing Problem
Staying in a high-pressure zone for a long time often leads to hearing problem.
Decompression Illness
The quick movement of welders from high to low-pressure regions can result in decompression illness. It can result in joint pain, muscle fatigue, weakness, and even death.
Hypothermia
Staying in water for a long time can cause excessive body heat loss and therefore, Hypothermia.
A career in underwater welding
It is evident from the above-mentioned section that underwater welding is a challenging and risky profession. It requires extreme physical and mental capacity along with skills to operate in extreme working conditions for a long time. Considering the working conditions, it may not be the best career option for most people.
However, maintaining safety precautions can reduce the possibility of damage or accidents. Among them, pre-diving equipment inspections, emergency Preparedness, and constant monitoring of the welding environment are of the highest importance.
However, underwater welding is obviously a lucrative job for those looking for a high salary. For example, an entry-level underwater welder gets approximately $32,000 per year in the USA. The salary range can rise up to $300,000 for the best welders depending on the experience, depth and diving method.
Do you need a certificate to be an underwater welder?
Underwater welding companies only employ certified welders. Most often companies require Underwater welders to possess certain skills, such as diving, Underwater cutting, oxyfuel welding, drafting, fitting and rigging, etc. These necessitate potential employees to receive professional training from commercial dive training institutions.
However, it is better to check if you are physically fit for the job before admitting to a school.
One may need the following certificates:
- Diving certificate
- Welding certificate
- Riggers certificate
Lastly
Many people want to be professional underwater welders, considering the high salary. Before starting the journey, it is crucial to have an overall idea about underwater welding. That’s why this article has focused on the basics of underwater welding, its process, advantages and career opportunities.
I hope the readers will find the information valuable for their practical use.