Pre-qualified welding procedure specifications (WPS) are standardized welding procedures that have been established and qualified in advance by recognized welding authorities or standards organizations. These pre-qualified procedures are based on extensive testing and documentation to ensure that they meet certain criteria for weld quality, strength, and reliability.
The purpose of pre-qualification is to streamline the welding process, save time and resources, while still ensuring to meet the required standards of the welds.
Codes and Standards
Not all welding codes offer the advantage of prequalified WPS. However, prominent standards like AWS D1.1 Structural Welding Code for Steel, AWS D1.3 for Sheet Steel, and AWS D1.6 for Stainless Steel extend this privilege.
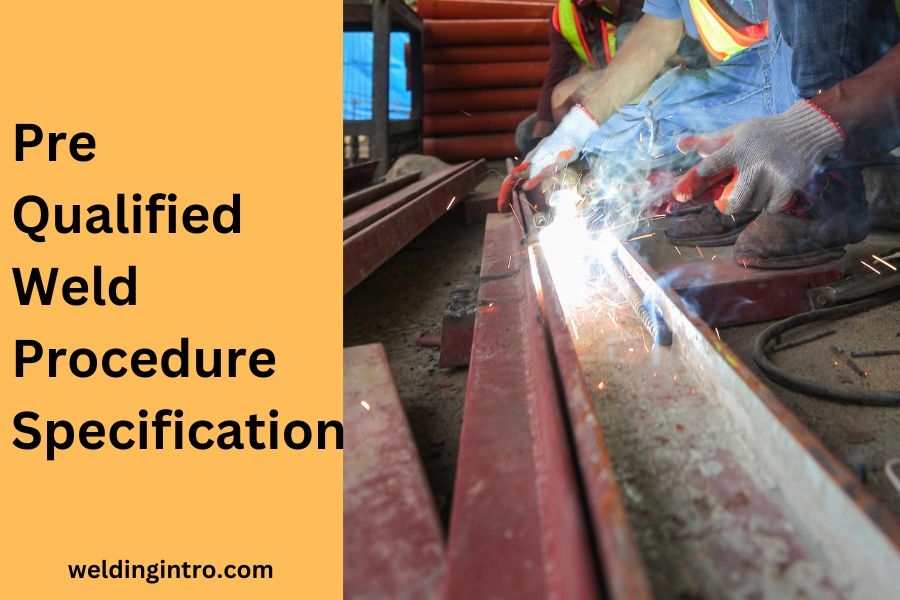
Key points of WPS
- Standardization: Pre-qualified WPS are standardized to cover common welding processes, materials, and joint configurations. This standardization helps ensure consistency in welding procedures across different projects and industries.
- Codes and Standards: Pre-qualified procedures are typically developed in accordance with established welding codes and standards, such as those set by organizations like the American Welding Society (AWS), the International Organization for Standardization (ISO), or other relevant industry bodies.
- Testing and Qualification: Before a welding procedure is pre-qualified, it undergoes rigorous testing to demonstrate its suitability for a particular set of conditions. This testing includes destructive (DT) and non-destructive examinations(NDT) to assess factors like weld strength, soundness, and integrity.
- Materials and Thickness Ranges: Pre-qualified procedures are often categorized based on the types of materials being welded and the thickness ranges of the components. This ensures that the procedures are suitable for specific applications.
- Joint Configurations: The pre-qualified procedures specify the types of joint configurations they are designed for, such as butt joints, fillet welds, groove welds, etc. This helps in selecting the appropriate procedure for a given welding project.
- Qualified Welders: Though the procedure itself is pre-qualified, it’s important to note that the welder performing the weld must also be qualified in accordance with the relevant standards. This may include testing their welding skills and knowledge to ensure they can execute the procedure correctly.
- Documentation: Detailed documentation accompanies pre-qualified WPS, outlining the specific parameters and conditions under which the procedure is valid. This documentation provides essential information for welders, welding inspectors, and other stakeholders involved in the welding process.
Advantages of Prequalified WPS
A Qualified Welding Procedure Specification (WPS) is a document that provides detailed instructions for welding a particular joint in a specific material using a qualified welding procedure. It is part of the broader Welding Procedure Qualification Record (WPQR) process.
The advantages of WPS are-
- Time Efficiency:
Since there are no testing requirements, prequalified WPS can be applied immediately, saving valuable time. It can be developed swiftly by following code requirements, eliminating the need for extensive weldment testing and waiting for several days for result.
- Cost Savings:
Qualification tests can be costly, with a single Procedure Qualification Record (PQR) ranging from $1,000 to $3,000. Prequalified WPS bypasses testing, resulting in significant cost savings, especially for multiple procedures.
- Enhanced Quality:
Prequalified WPS imposes strict welding requirements and limitations to ensure sound welds, contributing to overall weld quality control. However, welders skill and execution ability play a vital role in producing a quality weld.
4. Code Compliance:
Prequalified WPS is written in conformance with the applicable code, making it suitable for contracts requiring qualified welding procedures. Companies offering contracts must allow the use of prequalified WPS, as long as the relevant code permits it.
- Applicability Beyond Contracts:
Companies often develop prequalified WPS to meet contract requirements which can be applied to various projects. It leads to improved weld quality and reduce costs. It is not compulsory to be a welding engineer or inspector for writing the prequalified welding procedure specification. Anyone can write them as long as it comply with the codes.
Requirements and Considerations
Developing prequalified WPS requires a comprehensive understanding of the code’s requirements, including:
- Approved Joint Details:
Specify and adhere to approved joint configurations as outlined in the prequalified WPS. Ensure that the selected joint details are appropriate for the specific application and welding process.
- Filler Metal Parameters:
Use the filler metal manufacturer’s recommended parameters, including amperage, wire feed speed, volts, and Contact-to-Work Distance (CTTWD). Verify that the chosen filler metal aligns with the prequalified WPS and is suitable for the materials being welded.
- Allowed Welding Processes:
Identify and restrict the welding processes to those explicitly allowed for prequalification. For instance, some codes may prohibit certain processes, and it’s essential to comply with these restrictions. One example can be Using short circuit transfer GMAW is not allowed for WPS.
- Maximum Weld Sizes and Thicknesses:
Adhere to the maximum allowable sizes for single-pass fillet welds. Ensure compliance with limitations on root pass and fill pass thicknesses as specified in the prequalified WPS.
- Minimum Weld Sizes for Partial Joint Penetration (PJP) Welds:
Follow the guidelines for minimum weld sizes when executing partial joint penetration welds. Ensure that weld sizes meet the prequalified WPS requirements for PJP welds.
- Approved Filler Metals:
Use only approved filler metals specified in the prequalified WPS. Verify that the selected filler metals are compatible with the base materials and the welding process.
- Preheat and Inter pass Temperature:
Adhere to the requirements for preheat and inter pass temperature outlined in the prequalified WPS. Monitor and control temperature levels during welding to ensure compliance with specified parameters.
- Specified Travel Speeds:
Follow the travel speed recommendations provided in the prequalified WPS. Adjust travel speeds based on the welding process, materials, and joint configuration to meet specified criteria.
- Tolerances and Joint Details:
Adhere to the tolerances specified in the prequalified joint details. Ensure that the welding process complies with the defined tolerances for dimensions and other critical parameters.
- Comprehensive Understanding of Relevant Code Requirements:
Fully comprehend the requirements and limitations of the relevant welding code. Stay informed about any updates or changes to the code that may impact the use of prequalified WPS.
- Documentation and Record-Keeping:
Maintain accurate and up-to-date documentation of all prequalified WPS used in welding operations. Keep records of welder qualifications, equipment calibration, and any deviations from the prequalified procedures.
- Ongoing Education and Training:
Ensure that personnel involved in welding operations receive proper training and education on the use of prequalified WPS. Stay updated on industry advancements, enhances welding skills and knowledge.
- Regular Audits and Inspections:
Conduct regular audits and inspections to verify compliance with prequalified WPS. Address any deviations promptly and take corrective actions to maintain the integrity of the welding procedures.
SWPS Vs PWPS
It’s crucial to distinguish prequalified WPS from Standard Welding Procedure Specifications (SWPS).
- While prequalified WPS are exempt from qualification tests, SWPS must undergo testing.
- The latter is an option for applications that cannot be prequalified by any code, presenting a solution for unique scenarios, such as shielded metal arc welding (SMAW) of chromium-molybdenum steels.
Check the following video to learn more about WPS D1.1
https://www.youtube.com/watch?v=yIqsLJxrCsQ
Conclusion
While prequalified welding procedure specifications offer a streamlined approach to welding, it’s crucial to navigate the nuances of the relevant codes and standards. Efficiency and cost savings should not compromise weld quality.
Also thorough understanding of the requirements is essential for successful implementation of WPS. As we embrace the advantages of prequalified WPS, let’s remember that adherence to codes and standards is a foundation for quality, and continual optimization is key to achieving both excellence and productivity in welding practices.
Sources
- weldinganswers.com/what-is-a-prequalified-welding-procedure-specification
- welding-consultants-llc.myshopify.com/collections/aws-d1-1-prequalified-welding-procedure-specifications