Brazing
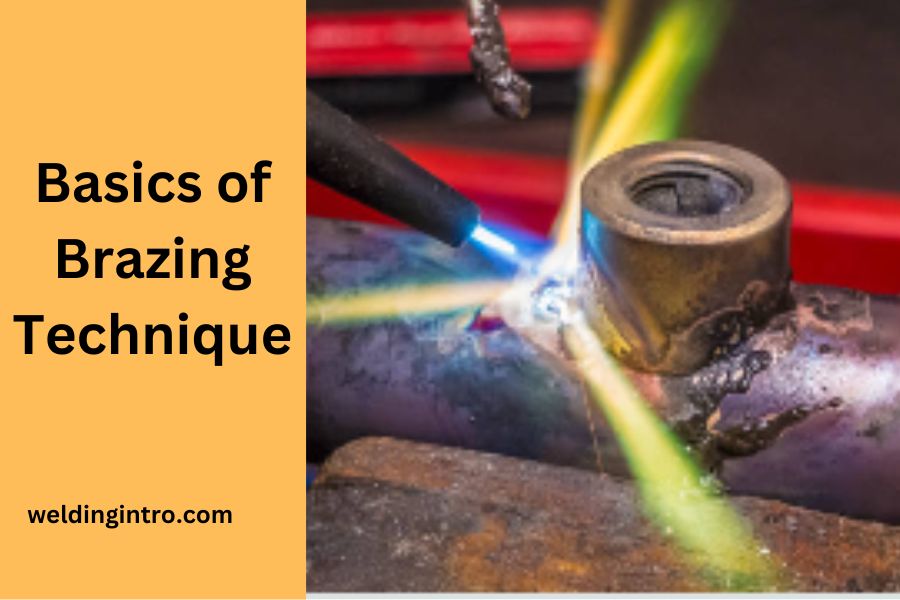
Brazing, a refined metal-joining technique, melts components with meticulous precision. Unlike welding, brazing employs a filler material with a lower melting point, typically above 450°C, to forge a robust bond between metals.
In short, Brazing is a process of melting filler alloy and flowing the molten filler rod into the joint of metals to be welded. As the filler material liquefies and solidifies, a seamless amalgamation emerges. This subtle process retains the structural integrity of the joined materials while allowing for intricate connections.
Here lower temperature is enough for solidifying the metal and that’s the point where it is different from all welding techniques available out there.
How Brazing Works
In brazing, a filler metal is required, which must have a lower melting point than the base metal and also it should be compatible with the base and workpiece metal. Then in a suitable atmosphere filler alloy metal is melted by applying heat on it. The atmosphere of brazing combines combustion fuel gas, nitrogen, air, ammonia, noble gasses, vapors or stems. These elements are used to create heating flames using a torch, furnace or induction coil.
When the heat from a torch or furnace melts the filler metal, it flows into the joint of metals to be joined. For sound brazing results, the metals should be cleaned with no rust on the surface and the gap between the metals should be designed in a way that the molten filler flows into that by capillary action.
At last when the molten filler solidifies and cools down, a strong and permanent bond is created. That’s how the brazing technique works.
Common Types of Brazing
There are several kinds of brazing techniques available. They are as follows-
- Furnace Brazing: This technique is versatile with a semi-automatic process. It is used in industrial projects. This process can be broken down into following types.
- Batch furnace
- Continuous furnace
- Retort Furnace
- Vacuum furnace
- Drop Brazing: This process is undertaken at an air-tight zone for preventing oxidation and after finishing the brazing, the assembly is dipped into salt water which works as a flux. Aluminum is brazed in this way most frequently.
- Silver Brazing: This process uses silver alloy as a filler metal to braze base metals. It is also known as hard soldering.
- Cast iron brazing: Here nickel is used as a filler rod to braze any metal. Copper can be used as filler metal for brazing underground pipes especially in the electric industry.
- Torch brazing: In this process, an automatic or semi-automatic torch is used to braze metals. This process has some types also. They are-
- Manual torch brazing
- Automatic torch brazing
- Machine torch brazing
Applications
Brazing is capable of joining two similar and dissimilar metals together without altering the properties of metals. However brazing can be used for the following projects.
- Tools Production: For making different types of tools like hammer, spades, surgical scissors, mining tools, knives, saw blades and drilling and evacuation instruments, brazing is used. It helps to join the metals together that make the shape of the tools.
- Automotive industry: For making structures, floor pans, exhaust systems, air conditioning parts, trailers and auto body parts, brazing is used. It ensures precision on the automobile parts joints.
- Jewelry Manufacturing: Brazing is used in jewelry making by joining different metal components together. It offers a precise and durable method for creating complex and decorative pieces crucial for jewelry making.
- Military and Defense: Components in military and defense equipment, such as missile components and vehicle parts, often undergo brazing to ensure the strength and reliability of the joints.
- Kitchen Appliances: Brazing is used in the manufacturing of kitchen appliances, including cookware and utensils, to create strong and durable joints.
- Plumbing and Pipe Fittings: Brazing is commonly used to join copper pipes and fittings in plumbing applications, providing a strong and leak-resistant connection.
- HVAC (Heating, Ventilation, and Air Conditioning): Brazing is employed in the fabrication of heat exchangers, refrigeration components, and air conditioning systems within the HVAC industry.
Selection of filler metal
Brazing is all about filler metal. If filler metal selection is wrong, the whole project can be ruined. To select the correct filler metal, you must follow the following factors.
- Use Copper-phosphorus (BCuP-X) alloy, if you are brazing copper to copper. Don’t use it in the connection of nickel and copper bases where the alloy contains more than 10% nickel.
- Use Aluminum-silicon (BAISi-X) alloy for joining aluminum to aluminum.
- Use Precious metals (BAu-X) for joining iron and cobalt.
- You may use Copper and copper-zinc alloy for joining silver, bronze, stainless steel, and copper.
- Use Magnesium (BMg-X) filler for magnesium-based alloys
Advantages
- The technique doesn’t alter the chemical properties of base metal as the base metal is not heated to melt.
- It is less costly process but stronger and precise
- Brazing excels in joining dissimilar metals, allowing for the creation of strong bonds between materials with different thermal expansion rates and melting points.
- Brazing occurs at lower temperatures compared to welding, reducing the risk of distortion, warping, or metallurgical changes in the joined materials.
- It doesn’t require an electric connection which saves energy and reduces the risk of accidents as well.
- Unlike welding, brazing doesn’t create a heat-affected zone, minimizing the impact on the surrounding material and preserving its original properties.
- Brazing equipment is generally less complex and more cost-effective than some welding setups, making it accessible to a wide range of applications.
- In medical applications, brazing can be performed using biocompatible filler materials, ensuring that the joints are safe for use in implants and medical devices.
Disadvantages
- In some applications, the joint strength achieved through brazing may be lower than that achieved by welding.
- Brazing is generally more suitable for joining thin-walled sections. It may not be the ideal choice for applications where thick sections need to be joined.
- The selection of suitable filler materials for brazing is critical, and not all materials can be brazed together. Compatibility issues may arise with certain metals or alloys.
- The joint built by brazing can take another hue. That is the joint can be of different color from base metal.
- Brazing typically does not achieve the depth of penetration seen in welding, which can affect the joint’s overall strength, especially in thicker materials.
- Brazing processes, especially in intricate or complex joints, may take longer compared to welding, potentially affecting production timelines.
Lastly
Brazing is easier and cost effective technique among welding techniques in the world. It creates seamless, clean and strong joint between metal pieces. All you need is a fuel backed torch and a filler metal to complete the job. The technique is very interesting and required less skill than other welding techniques. That’s why it is popular and practiced widely in the world.
Related Article