Water-cooled MIG guns provide a high level of performance for intensive welding tasks, affording you superior duty cycle and operator comfort.
These characteristics are particularly valuable in high-heat applications.

Comparison to Air-Cooled Systems
- Water-Cooled Guns utilize a cooling system that circulates water around the welding torch to dissipate heat more effectively than air-cooled counterparts.
This leads to a superior performance as they maintain a stable temperature even under high amperage. Which prolongs consumable’s life and increases weld quality.
- Duty Cycle: The duty cycle of water-cooled MIG guns is significantly higher compared to air-cooled systems.
It allows you to weld for longer periods without overheating the equipment, thereby boosting productivity.
- Flexible Cable Assembly: These types of MIG guns often come up with a flexible cable assembly, providing you with greater maneuverability during welding tasks.
- Comfort: The water cooling mechanism keeps the torch handle at a more comfortable temperature, reducing fatigue and the risk of burns during extended use.
Advantages of Water-Cooled Systems
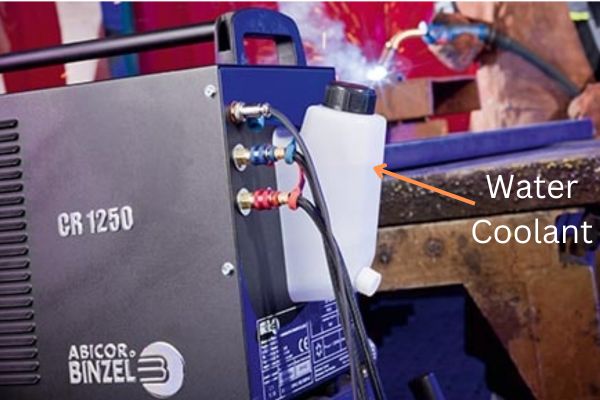
When you’re considering a water-cooled MIG gun, it’s important to understand the benefits this technology can bring to your welding projects. Here are some key advantages:
- Higher Duty Cycles: You can achieve higher duty cycles at the same amperage compared to air-cooled guns. This is crucial for projects requiring long, continuous welds.
- Reduced Overheating: The cooling effect allows you to work longer without the gun overheating. That ensures consistent performance and minimized downtime due to excessive heat.
- Lighter & More Flexible Cables: The cables on water-cooled guns are typically lighter and more flexible. So it is easy to manipulate the gun. This can reduce user fatigue and improve welding precision.
- Enhanced Performance for High Amperage: If your work requires high-amperage welding, water-cooled guns excel in sustaining that power and allows you to handle demanding applications.
- Longer Consumable Life: The water cooling system helps to extend the life of consumables such as tips and nozzles.
Components and Features
In this section, lets discover the essential components and features that make up a high-quality water-cooled MIG gun.
1. Design and Material Selection
When examining the design and material selection of water-cooled MIG guns, you’ll find that they’re built to handle extreme heat.
Often, the power cable and other cable assembly components are crafted from durable materials such as stainless steel to withstand the high-heat welding applications.
You’ll appreciate the thought that goes into the style of the gun, including the rear connector style. It ensures compatibility and ease of use with your welding setup.
Configurable industrial-duty semi-automatic water-cooled MIG guns typically feature customizable designs that cater to your specific welding needs.
2. Contact Tips and Nozzles
The contact tips and nozzles are critical components in conducting welding current and directing shielding gas, respectively.
It’s essential to have a robust & precise contact tips as they directly affect the quality of your weld.
The nozzles, on the other hand, must be shaped to help maintain access to your workpiece while offering protection from the intense welding environment.
Features like a conduit liner, that aligns perfectly with the tips and nozzles, are vital for preventing wire feeding issues. It also ensures smooth operation throughout your welding projects.
Technical Specifications
In the world of welding, your equipment’s performance hinges on its specifications.
Especially with a water-cooled MIG gun, understanding its technicalities, like gun ratings and duty cycle, as well as cable and connector options, is vital for making the right choice for your welding needs.
1. Gun Ratings and Duty Cycle
The duty cycle of a water-cooled MIG gun tells you how long you can weld at a specific amperage before needing to rest the gun to prevent overheating. For example, a Standard 600 Water Cooled MIG Gun operates at a 600 AMP with 100% duty cycle, meaning it can run continuously at full capacity.
- Maximum Duty Cycle: 100% at rated amperage
- Example Ratings: 500 A CO2, 450 A mixed gases
Heavy-duty copper components ensure that conductivity and cooling system are optimized for prolonged use at high power input.
2. Cable and Connector Options
The flexibility and durability of your MIG gun’s cable are also paramount for efficient operation. A flexible cable helps reduce fatigue and allows for ease of movement, which can be critical during long welding sessions.
- Cable Types: Reinforced synthetic rubber hoses
- Connector Varieties: Tweco style and Euro-connectors
Water-cooled MIG guns with high-quality, durable connectors facilitate a reliable transfer of power and shielding gas. They also contribute to the overall duty cycle reduction due to efficient energy transfer, reducing the need for pauses in operation.
Operational Excellence
Operational excellence hinges on two pivotal aspects: a) how comfortably you can handle your welding tool and b) how effectively you can maintain it for peak performance.
Both ergonomics and maintenance play crucial roles in the overall productivity and longevity of your MIG gun.
1.Ergonomics and Handling
You’ll notice a significant difference in your welding experience with the ABICOR BINZEL water-cooled MIG guns, which are designed to provide optimal comfort.
Long hours of welding in a production environment can lead to excessive heat, potentially causing discomfort and heat overexposure.
With the water-cooling technology, your MIG gun stays at a manageable temperature, keeping your hands cool and comfortable.
- Lightweight: The reduced weight minimizes hand fatigue.
- Flexible: A repairable power cable allows for easier manipulation.
2. Maintenance
Maintaining a water-cooled MIG gun is pivotal for ensuring top-tier performance in production environments.
Regular upkeep of components like the Bernard T-Gun series or the Miller M-25 gun ensures they’re ready to face challenging conditions without costly interruptions.
- Cooling system: Check the coolant levels and signs of leaks regularly.
- Nozzles and tips: Replace as needed to maintain quality welds.
By focusing on ergonomic design and diligent upkeep, your water-cooled MIG gun will deliver sustained operational excellence, making your welding tasks more comfortable and your results more consistent.
Frequently Asked Questions
In this section, we’ll explore some of the common inquiries you may have regarding water-cooled MIG guns.
1. What are the advantages of using a water-cooled MIG gun instead of an air-cooled one?
A water-cooled MIG gun can handle higher amperages and longer welding durations by efficiently dissipating heat.
This results in less downtime and can improve productivity, especially on high-amp industrial jobs.
Water-cooled MIG guns are also generally lighter and more flexible, reducing operator fatigue.
2. How does a water-cooled MIG torch improve the welding process?
The cooling system in a water-cooled MIG torch can sustain a consistent temperature, even during high-heat welding operations.
This steady temperature helps maintain the quality and consistency of the welds, which is particularly important in precise applications.
3. Can you explain the maintenance requirements for a water-cooled MIG gun?
Maintenance for a water-cooled MIG gun involves regular checks for leaks in the cooling system. Also regular checking of the coolant level and concentration, and occasional flushing the system to remove any build-up is necessary for longer life of mig torch.
Proper maintenance ensures optimal gun performance and longevity.
4. How do push-pull welding guns compare to water-cooled MIG guns in terms of performance?
Push-pull welding guns are designed for welding with soft wires like aluminum, which need careful feeding through the gun to prevent jamming.
In terms of performance, they’re not directly comparable to water-cooled MIG guns, which are focused more on heavy-duty welding that requires effective cooling.
Each has features that suit different welding requirements.