Flux core vs. stick welding– wondering which welding process is suitable for the project in hand?
They are both versatile and popular welding techniques in the industry. However, there are a few variations when it comes to performance, deposition rate, the voltage used, and formation of gaseous substances.
If you are reading this article, you are either a welder yourself or just started your journey in the field. Regardless, there are a lot to learn here.
So, lets start with
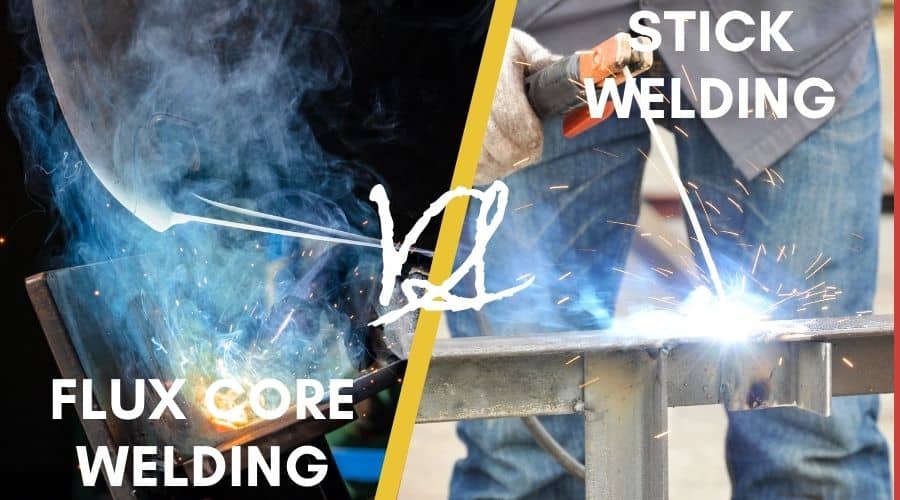
Flux Core Arc Welding
Flux Core Arc Welding (FCAW) is also known as dual shield welding. Basically, it is an arc welding process that has similarities with Metal Active Gas (MAG) welding process. FCAW uses constant wire-fed electrodes with a continuous voltage supply to fuse metal at intersections.
Overview of FCAW Welding Processes
FCAW can be automatic or semi-automatic. The filler wire in this process is vacant and filled with flux.
In the welding process, the flux protects and covers the weld pool, so the gas does not have to shield the weld. Because of this proceeding, the weld cools faster and becomes more anchored.
Advantages
- FCAW has been able to overcome various restrictions prevalent with MMA welding since it uses constant wire-fed electrodes.
- It is a high-yielding procedure for alloy, plain carbon, duplex and stainless steels.
- It is particularly suitable for shipbuilding, common repairs, underwater welding, pipeline welding, and other manufacturing work.
- The coating cools quickly making the weld more stable.
- The tube-shaped electrodes prevent atmospheric particles from contaminating the melt.
- Since you don’t have to carry a tank during the welding process, FCAW is more convenient.
- It is suitable for bigger projects as a good price flux-core welder can dispatch 25 pounds of wire per hour compared to 8 pounds per hour by a (Metal Inert Gas) MIG.
Disadvantages
- Despite its usability, FCAW produces a high dose of toxic fumes that pose danger to the welder and his immediate environment.
- The tubular wire electrodes used here are costlier than regular electrode wires.
- Even the equipment needed to operate FCAW is costlier than other regular tools.
- Although the welder gets a mobility advantage, FCAW is still less portable and flexible than Gas Tungsten Arc Welding (GTAW) or Shielded Metal Arc Welding (SMAW).
- There is a limitation imposed on the type of metal you can weld with this technique.
- If you encounter mechanical issues, it can result in porosity of the weld, inconsistent wire feed, and thawed contact tips.
Optimization and Performance
The FCAW is known to supply greater penetration than other types of welding proceedings. That is why it is widely used in melding thick joints.
Furthermore, it allows the welder to move in various directions during welding due to its mobile nature. Hence, portability and ease of movement result in optimization of performance.
The welder does not need to be highly skilled either. Performing FCAW is quite easy to learn and operate on machinery.
What is Stick Welding
Stick welding has different names in the welding world. It can be also known as Shielded Metal Arc Welding (SMAW), manual metal arc welding, manual electrode welding, or manual arc welding. In fact, it is a beginner’s welding process that all welders are familiar with.
Overview of Welding Processes SMAW
This welding process requires the electrode to carry the current to the metal object. When the tip of the electrode comes in contact with the surface of the metal, the heat melts the metal and rod to form the weld.
Once the flux skin vaporizes, it turns into gas and slag in order to shield the weld from outer pollutants. To finish off the welding process, the welder chips away from the slag.
Advantages
- It is easy to learn for beginners of welding.
- SMAW is used in the metal, steel, and pipe industry for construction and repair.
- The welder can work this process even in rain and wind.
- He does not need any shielding gas during the welding task, so you save some money there.
- Equipment and tools used in SMAW are not as expensive as FCAW.
- At the welding point, this welding procedure is not sensitive to dirt, corrosion, and paint. Therefore, the clean-up process is effortless.
Disadvantages
- The process may be slower than other welding techniques.
- Although clean-up is minimized from paint, dirt, and corrosion, it takes time to remove the slag formed after welding.
- Rough surfaces, smears, and porosity are common with this type of welding.
- Even though you can change the rods for different metals, they may have to be replaced frequently.
- SMAW is not recommended for thinner metals.
Optimization and Performance
Stick welding or SMAW is considered to be stronger than MIG since it can perforate thicker materials. Even though you can do perform SMAW in the rain, it is still quite dangerous. Accidents from mistakes and electrical shocks are some of the issues that may hamper progress.
Being a beginner-friendly welding process, SMAW is popular with welders of all levels. The techniques are simple and easy to learn as well.
What Can FCAW and Stick Weld?
The materials that can be welded by FCAW are carbon steel, low-alloy steel, cast iron, high-nickel alloy, and stainless steel.
On the other hand, SMAW can weld ductile iron, cast iron, low alloy steel, high alloy steel, carbon steel, and stainless steel. This process can weld any of these metals that are ⅛ inch or thicker.
Flux Core vs. Stick Welding: Know the Differences
Flux Core (FCAW) Welding | Stick (SMAW) Welding | |
Portability | Good | Good |
Resistance to Bad Weather | Good | Good |
Skill Needed | Easy and affordable to learn | Easy to learn |
Penetration | High | High |
Deposition Rate | 8 to 25 pounds per hour | 3 to 5 pounds per hour |
Energy Source | DC or AC electric arc | AC/DC transformer rectifier, AC transformer, DC generator/inverter, and DC rectifier |
Voltage | 25 to 26 volts | 22 to 27 volts |
Feeding Process | Continous wire-fed tubular electrodes | Heat arc melts the top base of the metals and electrodes |
Smoke Generation | Produces noxious smoke during welding | High levels of metal and fluoride gas |
Cost of Machinery | High | Medium |
Weldable Materials | Cast iron, stainless steel, low alloy steel, carbon steel, and nickel alloy | Ductile iron, cast iron, high/low alloy steel, carbon steel, and stainless steel |
Which One Should You Use
Now a big question arises and that is which one welding process should you go for. Lets find out the answer in detail.
Why You Should Go for Flux-Cored Welding
Flux-core welding is the most effective and efficient welding process that exists right now. It overcomes all the problems and restrictions faced by other types of welding proceedings.
The welding coat dries out quickly with this type of welding process. The weld is also protected from atmospheric contaminants for a cleaner finish.
It is also portable and convenient without having to carry a gas tank around. Most importantly, it has a high deposition rate and feeding process.
Why You Should Go for Stick Welding
Although as not as good as the flux-core welding process, stick welding or SMAW is easier to learn. This welding technique can be used in bad weather conditions, like wind and rain, as well.
You save a significant amount of money with stick welding since it does not need any shielding gas during the welding process. The equipment used for this is also not as pricey as the ones for FCAW.
Additionally, cleaning up after the welding is simple as this process is not sensitive to erosion, stain, and pollution.
(FAQ) Frequently Asked Questions
I’m pretty sure there are other questions swarming in your mind. So, here are some answered ones!
1. How Much Faster is Flux Cored Arc Welding?
Flux Core Arc Welding is the most high-yielding welding process. It can be automatic or semi-automatic, and its production rate is extremely high. The deposition rate of FCAW is 8 to 25 pounds per hour, which is higher than other welding processes.
2. Why Dual Shield Flux Core is Faster Than Stick?
A Dual Shield Flux Core or FCAW is quicker than the stick welding process because DSFC welding uses a number of wire-speed feed and voltages. It does not stop to change rods, plus there is a higher deposition rate compared to stick welding.
3. What Types of Electrodes Can Be Used with FCAW?
FCAW uses tubular wire that is constantly fed with metal and metal oxide powders. These powders eventually create a slag over the weld for protection.
To Reach a Conclusion
That was a lot of information to process. If you are a trained welder, you must already be familiar with the basic procedures involved with these two types of welding. This article just filled up the missing puzzles in your head.
Moreover, if you are wondering which process is suitable for your project, you read them, right?
FCAW is ideal for bigger projects, whereas SMAW is suitable for smaller ones. Material-wise, SMAW and FCAW can weld stainless steel, cast iron, high alloy steel, low alloy steel, cast iron, and carbon steel.
The thicker the material, the better to use FCAW. But be mindful of the cost though. Likewise, apply the SMAW technique on thinner materials at an affordable price range.
Related Article