Welcome to the fascinating realm of welding, where the fusion of metals transforms imagination into tangible structures. In this article, we embark on a journey to unravel the diverse tapestry of welding techniques, exploring the unique characteristics and applications of each.
Whether you’re a novice welder or a seasoned pro, there’s always something new to discover in the vast landscape of welding.
Types of Welding
We can divide the welding techniques into 6 basic categories. They are
- Solid State welding
- Resistance welding
- Arc welding
- Oxy-fuel welding
- Brazing
- Soldering
Here each of the categories have subdivisions. And can be divided into multiple more types.
Among them arc welding is the most diverse and popular form of welding which can be divided into seven more parts. However we will discuss the basic types of welding here. Let’s start
Solid State Welding
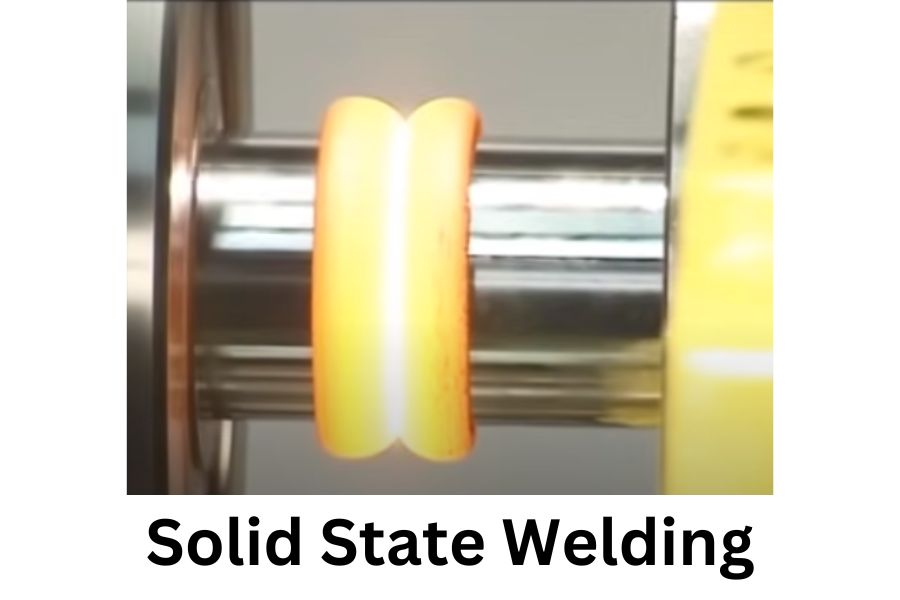
Solid state welding is a family of welding techniques that forge metal joints without melting the materials involved. Unlike traditional methods that involve melting and then solidifying the metals, solid state welding achieves bonding through mechanical pressure, heat, or both. This innovative approach results in superior structural integrity and minimizes distortions and defects commonly associated with fusion-based welding.
Pros
- High Strength Bonds: Solid state welding produces joints with exceptional strength, often surpassing the parent materials.
- No Melting: The absence of melting eliminates the risk of thermal distortion and reduces the likelihood of metallurgical defects.
- Precise Control: This technique allows for precise control over the welding process, making it suitable for intricate projects.
- Environmentally Friendly: With no need for filler materials or shielding gases, solid state welding is environmentally friendly.
Cons
- Equipment Cost: Specialized equipment for solid state welding can be expensive, limiting accessibility for some workshops.
- Material Compatibility: Certain materials may have limitations in terms of weldability with this technique.
- Process Time: Solid state welding can be time-consuming, making it less suitable for high-volume production.
Projects
- Solid state welding is employed in manufacturing critical aerospace components, ensuring lightweight yet robust structures.
- This technique is used to create joints in automotive parts where high strength and precision are paramount.
- In the realm of microelectronics, solid state welding is applied for bonding small-scale components, ensuring reliability in delicate devices.
In summary, solid state welding stands as a cutting-edge welding technique with remarkable benefits in terms of strength, precision, and environmental impact. While the initial investment and time considerations may pose challenges, the technique’s advantages make it a compelling choice for projects where uncompromising quality is non-negotiable.
Resistance Welding
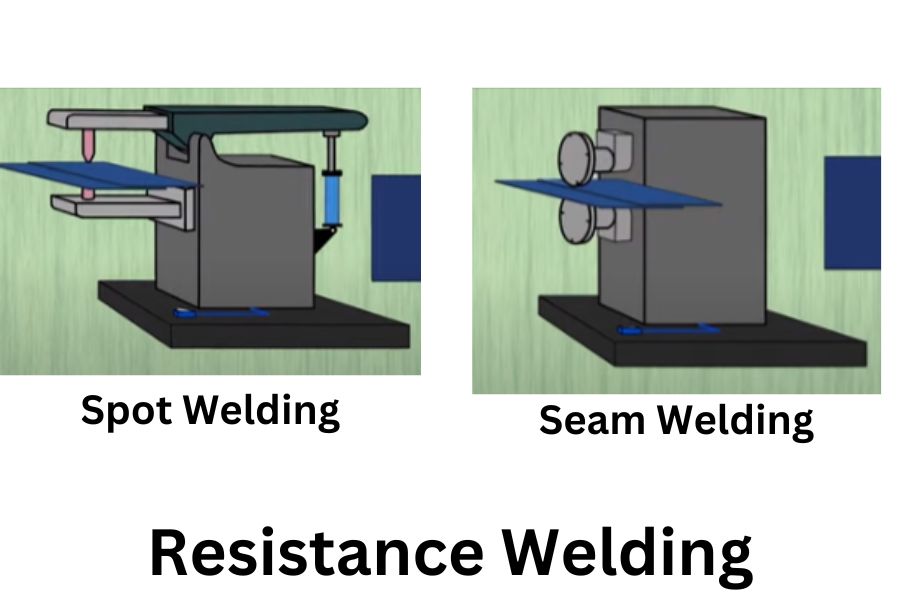
Resistance welding is a widely-used welding technique that joins metals by applying pressure and passing a high electric current through the workpieces. This method relies on the natural resistance of metals to electric current, generating heat at the interface and causing the materials to fuse together.
This process is notable for its speed, efficiency, and suitability for high-volume production.
Pros
- Speed and Efficiency: Resistance welding is a rapid process, making it ideal for mass production applications.
- No Filler Materials: The process doesn’t require additional filler materials, reducing costs and simplifying the welding setup.
- Localized Heating: Precise control over heat application allows for localized heating, minimizing thermal distortion.
- Versatility: Suitable for a wide range of metals, including steel, aluminum, and copper.
Cons
- Equipment Complexity: Specialized machinery is required, and initial setup costs can be relatively high.
- Limited Thickness Range: Best suited for thin to medium thickness materials; may face challenges with extremely thick metals.
- Joint Accessibility: Restricted to areas where the electrodes can be positioned for effective current flow.
Projects
- Resistance welding is extensively used in the automotive industry for joining components like body panels and exhaust systems.
- Common in the production of consumer electronics, where it creates precise, reliable joints in components.
- Ideal for manufacturing metal furniture, providing quick and strong connections in components like frames and brackets.
In conclusion, resistance welding is a versatile and efficient method, particularly well-suited for applications demanding high-speed production and consistent joint quality. Despite some equipment complexities, its widespread use in industries such as automotive and electronics attests to its effectiveness in creating durable and reliable metal joints.
Arc Welding
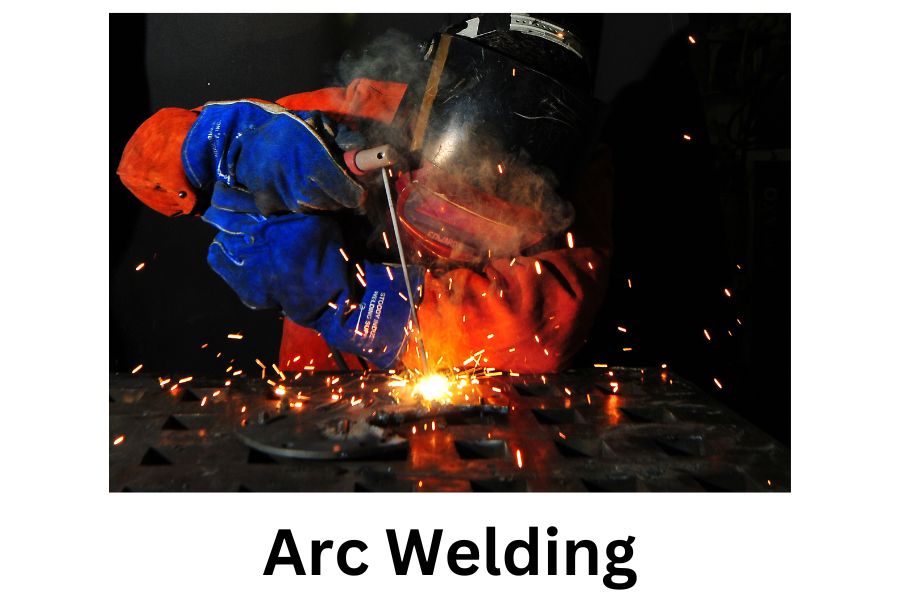
Arc welding is a versatile and widely-used welding technique that employs an electric arc to melt and fuse metals. This process involves creating an intense electrical discharge, or arc, between an electrode and the workpiece, generating the heat required for melting. Arc welding encompasses various methods, including Shielded Metal Arc Welding (SMAW), Gas Metal Arc Welding (GMAW/MIG), and Gas Tungsten Arc Welding (GTAW/TIG).
Pros
- Versatility: Arc welding can be applied to a wide range of metals and alloys, making it a flexible choice for various projects.
- Portability: Methods like SMAW are portable and suitable for outdoor welding, providing flexibility in project locations.
- Cost-Effective: Initial equipment costs are relatively lower compared to some other welding techniques.
- High Penetration: Arc welding can achieve deep penetration, resulting in strong and durable welds.
Cons
- Spatter and Fumes: Arc welding can produce spatter and fumes, requiring adequate ventilation and safety measures.
- Skill Dependence: Achieving quality welds demands a certain level of skill and experience from the welder.
- Joint Cleanup: Welds may require post-weld cleaning and finishing to achieve desired aesthetics.
Projects
- Arc welding is extensively used in the construction of buildings, bridges, and other infrastructure projects.
- Its versatility and penetration capabilities make arc welding crucial in the construction of ships and marine structures.
- Common in the manufacturing of vehicles, arc welding creates sturdy connections in automotive frames and components.
In summary, arc welding remains a cornerstone in the welding industry, offering a balance of versatility, accessibility, and cost-effectiveness. Its applications span across diverse sectors, making it a reliable choice for both large-scale industrial projects and smaller-scale fabrication tasks.
Oxy-Fuel Welding
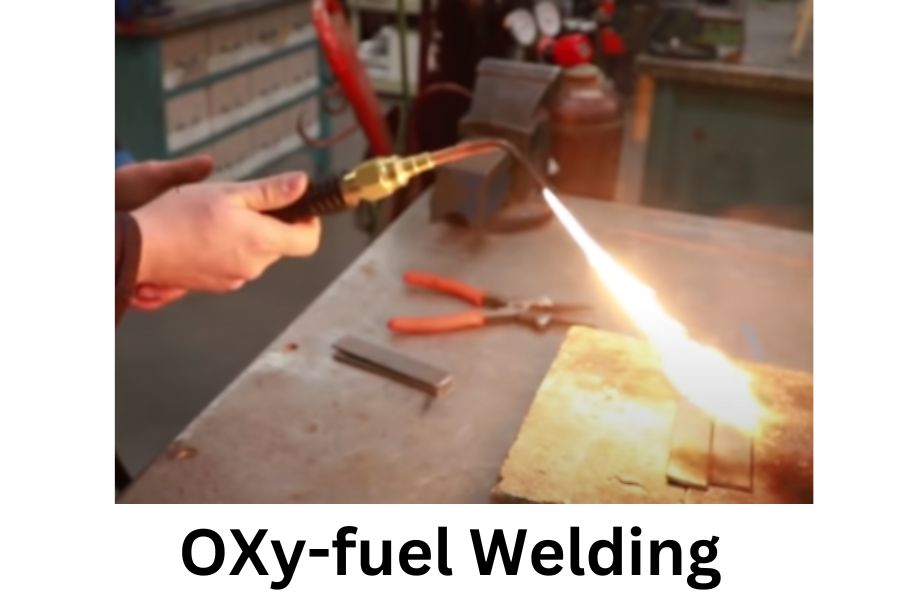
Oxy-fuel welding, also known as gas welding or oxyacetylene welding, is a traditional yet effective technique that employs the combustion of oxygen and a fuel gas, typically acetylene, to generate intense heat for metal joining. This versatile method is celebrated for its simplicity and remains a valuable skill in various industries.
Pros
- Portability: Oxy-fuel welding equipment is portable, allowing for flexibility in project locations, especially in field repairs and construction sites.
- Versatility: This technique is suitable for a wide range of metals and thicknesses, making it adaptable for various welding applications.
- Low Equipment Cost: Initial setup costs are relatively low compared to some other welding methods.
- No Electricity Required: Oxy-fuel welding can be performed without access to electricity, enhancing its applicability in remote areas.
Cons
- Limited Precision: Achieving high precision can be challenging compared to some modern welding methods.
- Heat-Affected Zone: The process may result in a larger heat-affected zone, potentially affecting the mechanical properties of the metal.
- Safety Concerns: Acetylene is a highly flammable gas, requiring careful handling and storage to ensure safety.
Projects
- Oxy-fuel welding is embraced by artists and sculptors for its hands-on approach, enabling them to create intricate metal sculptures.
- Used for joining pipes in pipeline construction, taking advantage of its portability and adaptability to different metal thicknesses.
- Common in small-scale automotive repairs and fabrication due to its simplicity and accessibility.
In conclusion, oxy-fuel welding may be considered a classic technique, but its versatility and cost-effectiveness make it a valuable tool in various welding applications, particularly in scenarios where portability and adaptability are crucial.
Brazing
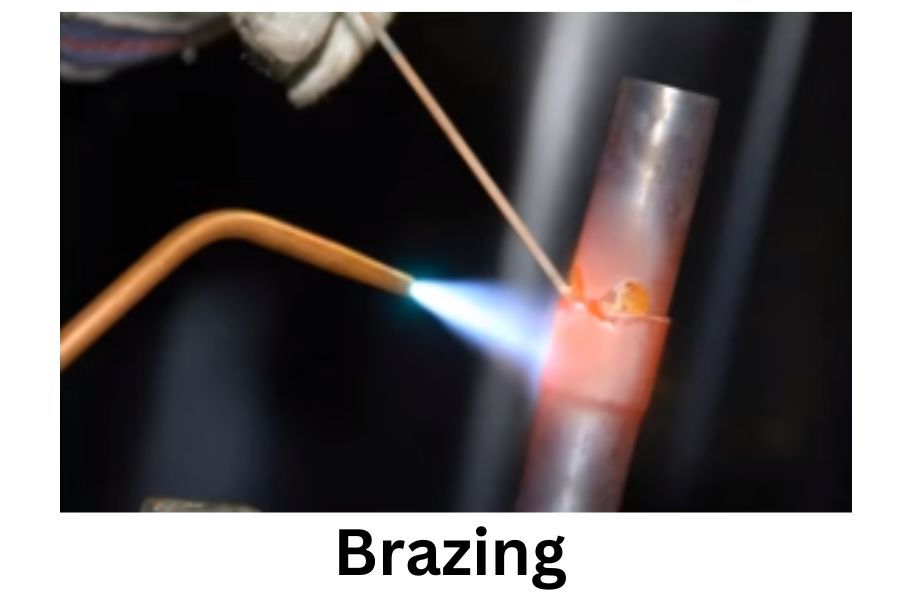
Brazing is a metal-joining technique that utilizes a filler metal, typically in the form of a rod or wire, to create a strong bond between workpieces. Unlike welding, brazing occurs at temperatures above 450°C (842°F) but below the melting point of the base metals. This allows for precise and clean joints with minimal thermal distortion.
Pros
- Versatility: Brazing accommodates a wide range of metals, including dissimilar materials, promoting versatility in project applications.
- Joint Aesthetics: The process results in clean and aesthetically pleasing joints, often with minimal post-weld cleanup.
- Lower Thermal Distortion: Brazing operates at lower temperatures than welding, minimizing thermal distortion and reducing the risk of metallurgical changes.
- Joining Dissimilar Metals: Ideal for joining metals with significantly different melting points or thermal expansion rates.
Cons
- Lower Joint Strength: Generally, brazed joints may have lower strength compared to fully-welded joints.
- Not Suitable for High-Stress Applications: Brazing may not be suitable for applications requiring high structural integrity and load-bearing capacity.
- Limited Penetration: The process may not penetrate materials as deeply as some welding techniques.
Projects
- Brazing is commonly used in crafting intricate jewelry, ensuring precise and clean joints in metalwork.
- Widely employed in the manufacturing of heat exchangers due to its ability to join dissimilar metals efficiently.
- Brazing is utilized in the aerospace industry for its ability to create strong joints in lightweight materials.
In summary, brazing stands as a meticulous and versatile technique, offering advantages in joint aesthetics and compatibility with various metals. While not suitable for all applications, its precision makes it an excellent choice for projects where the visual appeal of joints and versatility are paramount.
Soldering
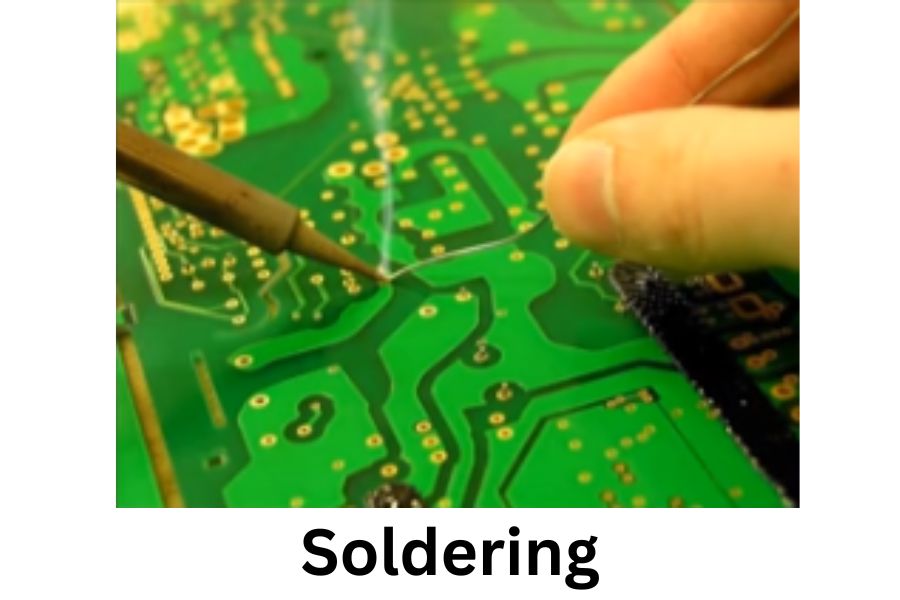
Soldering is a low-temperature metal-joining technique that utilizes a filler metal, known as solder, to create strong, electrically conductive bonds between workpieces. Operating at temperatures below 450°C (842°F), soldering is distinguished by its ability to join metals without melting the base materials. This technique is widely employed for electronic and delicate metalwork applications.
Pros
- Low Heat Application: Soldering’s low temperatures prevent thermal distortion, making it suitable for delicate components and electronic circuits.
- Clean Joints: Soldering produces neat and clean joints, enhancing the aesthetic appeal of the finished work.
- Electrical Conductivity: Soldered joints exhibit excellent electrical conductivity, crucial for electronic applications.
- Versatility: Soldering can join a variety of metals, facilitating versatility in project applications.
Cons
- Lower Mechanical Strength: Soldered joints may not be as mechanically robust as those created through welding or brazing.
- Material Limitations: Soldering is most effective with materials that have compatible melting points, limiting its use in certain applications.
- Not Suitable for Load-Bearing Structures: Due to its lower mechanical strength, soldering is not ideal for projects requiring high load-bearing capacity.
Projects
- Soldering is a cornerstone in electronic manufacturing, used to join components on circuit boards.
- This technique is prevalent in crafting jewelry, allowing for precision in bonding delicate metals.
- Commonly used for joining pipes and fittings in plumbing applications where high temperatures could damage other materials.
In conclusion, soldering’s gentle touch and electrical conductivity make it indispensable in industries where delicate and precise metal bonding is paramount. While not suitable for all applications, its unique advantages make it a valuable tool in crafting intricate and technologically advanced projects.
FAQ (Frequently Asked Questions)
1. Can you explain the concept of “solid state welding”?
Solid state welding encompasses techniques like friction welding and ultrasonic welding, where metals are joined without melting. This process ensures minimal thermal distortion, making it ideal for precision work. It relies on mechanical pressure, heat, or both to create a strong bond between materials.
2. Can you provide examples of projects where Arc Welding is the preferred technique?
Arc Welding, with its versatility and ability to handle various metals, is preferred in construction for welding structural components, in shipbuilding for joining metal plates, and in automotive fabrication for creating robust connections in vehicle frames and components. Its adaptability makes it a staple in numerous large-scale projects.
3. How does Resistance Welding contribute to the automotive manufacturing process?
Resistance Welding plays a crucial role in the automotive industry by efficiently joining sheet metal components in the production of vehicles. Its speed and ability to create strong, localized welds make it an integral part of the automotive manufacturing process.
4. What are the advantages of Brazing over traditional welding methods?
Brazing offers advantages such as cleaner joints, versatility in joining dissimilar metals, and the ability to work with delicate materials. Its lower temperature requirements prevent thermal distortion, making it a preferred method for applications where aesthetics and precision are critical.
5. How does Oxy-Fuel welding differ from other heat-based welding methods?
Oxy-Fuel welding, or gas welding, uses the combustion of oxygen and acetylene to generate heat for joining metals. Its portability and versatility make it suitable for projects in various locations, and it stands out in applications where low-temperature welding is crucial, such as in delicate metalwork.
6. What are the primary applications of Resistance Spot Welding (RSW)?
Resistance Spot Welding is widely used in the automotive industry for joining sheet metal components in the manufacturing of cars. The process involves applying pressure and passing a high electric current through the metal sheets, creating localized welds with high structural integrity.
Lastly
There are many more types of welding techniques and each of them are unique and very useful for life. Modern world wouldn’t exist if welding techniques were not discovered. As a beginner one must know about the welding techniques and their use.
Also Read
Resources